Crane telescoping control device
A telescopic control and crane technology, which is applied in the direction of cranes, fluid pressure actuating devices, mechanical equipment, etc., can solve problems such as failure to work normally, failure of normal telescopic or recovery of the boom, and impact on the safety of crane operations, so as to save manpower and the effect of input cost, small changes, and safety of maintenance personnel
- Summary
- Abstract
- Description
- Claims
- Application Information
AI Technical Summary
Problems solved by technology
Method used
Image
Examples
Embodiment Construction
[0015] Such as Figures 2 to 3 shown
[0016] The control device includes an emergency control valve group 1 , and the emergency control valve group 1 includes a first electromagnetic reversing valve 11 and a second electromagnetic reversing valve 12 .
[0017] The first electromagnetic reversing valve 11 includes oil port P1, oil port T1, oil port A1 and oil port B1. The oil port P1 of the first electromagnetic reversing valve 11 is connected with the oil circuit of the telescopic oil cylinder 4. The first electromagnetic reversing valve The oil port T1 of 11 communicates with the oil circuit of the telescopic oil cylinder 4 through the one-way valve 13, and the one-way valve 13 restricts oil from moving from the oil port T1 of the first electromagnetic reversing valve 11 to the oil circuit direction of the telescopic oil cylinder 4;
[0018] In normal state, port P1 of the first electromagnetic reversing valve 11 is connected to port B1, and port A1 is connected to port T1....
PUM
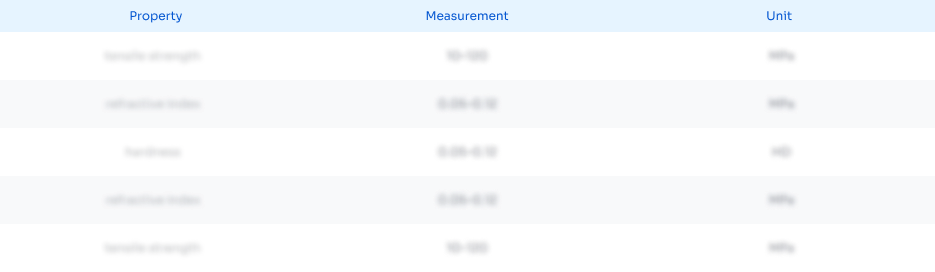
Abstract
Description
Claims
Application Information

- Generate Ideas
- Intellectual Property
- Life Sciences
- Materials
- Tech Scout
- Unparalleled Data Quality
- Higher Quality Content
- 60% Fewer Hallucinations
Browse by: Latest US Patents, China's latest patents, Technical Efficacy Thesaurus, Application Domain, Technology Topic, Popular Technical Reports.
© 2025 PatSnap. All rights reserved.Legal|Privacy policy|Modern Slavery Act Transparency Statement|Sitemap|About US| Contact US: help@patsnap.com