Constant force adjustable multi-degree-of-freedom flexible micro-gripper
A degree of freedom and micro-clamping technology, applied in the direction of workpiece clamping devices, manufacturing tools, etc., can solve the problems that the micro-gripper cannot output constant force, aggravate the deflection of the object being operated, and cannot change the constant force, etc., to achieve machining accuracy Easy to secure, light in structure and easy to operate
- Summary
- Abstract
- Description
- Claims
- Application Information
AI Technical Summary
Problems solved by technology
Method used
Image
Examples
Embodiment Construction
[0035] The specific embodiments of the present invention will be described in further detail below in conjunction with the accompanying drawings. It should be noted that the specific embodiments are only specific illustrations, not limitations of the present invention.
[0036] The invention provides a multi-degree-of-freedom flexible micro-gripper with adjustable constant force, including a micro-clamping unit, such as figure 1 As shown, the micro-clamping unit includes a clamping part 6 and a degree of freedom adjustment part, and the clamping part 6 is installed on the degree of freedom adjustment part and can be driven by the degree of freedom adjustment part in three directions: up and down, left and right, and front and back. Move, the clamping part 6 is connected with the degree of freedom adjustment part through a connecting block 8, and the degree of freedom adjustment part is fixed on the different-plane base 9 through the base 1, so that the degree of freedom adjustm...
PUM
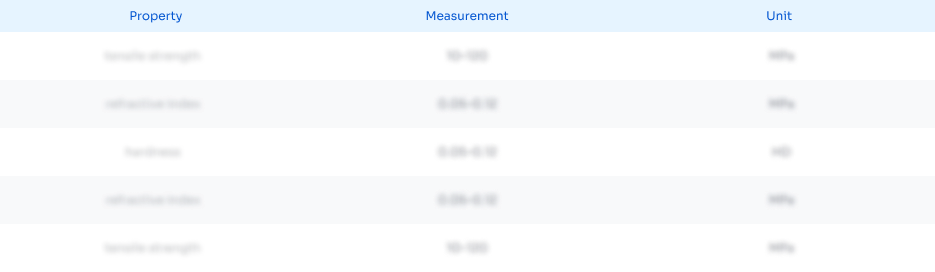
Abstract
Description
Claims
Application Information

- R&D
- Intellectual Property
- Life Sciences
- Materials
- Tech Scout
- Unparalleled Data Quality
- Higher Quality Content
- 60% Fewer Hallucinations
Browse by: Latest US Patents, China's latest patents, Technical Efficacy Thesaurus, Application Domain, Technology Topic, Popular Technical Reports.
© 2025 PatSnap. All rights reserved.Legal|Privacy policy|Modern Slavery Act Transparency Statement|Sitemap|About US| Contact US: help@patsnap.com