A kind of preparation method and application of lignin modified product
A technology of modified substances and lignin, which is applied in the field of lignin reuse and re-application, can solve the problems of poor structural regularity of graft copolymers, poor functional consistency of modified polymers, and difficult control of the reaction process, etc., to achieve improved The effects of applying added value, alleviating resource crisis, and improving utilization
- Summary
- Abstract
- Description
- Claims
- Application Information
AI Technical Summary
Problems solved by technology
Method used
Image
Examples
Embodiment 1
[0040] The preparation method of lignin-DMC graft copolymer: add a certain amount of alkali lignin in the electrolytic cell, add an appropriate amount of deionized water to dissolve, adjust the required pH, and then add a certain amount of DMC, the concentration of alkali lignin is 10g / L, alkali lignin: DMC ratio of 1:9, heated in water bath to the required temperature of 70°C, stirred with a magnetic stirrer (rotating speed 200 r / min), inserted anode and cathode electrodes (the effective area of anode and cathode is 3.5 cm×4 cm respectively , the distance between the two electrodes is 5 cm), turn on the power button, adjust the voltage to 2.5v, let the lignin graft copolymerization reaction start, the reaction time is 6h, after the reaction, the sample is in ethanol with a mass fraction ≥75% Precipitate, let it stand for enough time, after the precipitation is completely settled, pour off the supernatant, leave the precipitate, wash the copolymer twice with ethanol with a m...
Embodiment 2
[0042] The preparation method of lignin-DMC graft copolymer: add a certain amount of alkali lignin in the electrolytic cell, add an appropriate amount of deionized water to dissolve, adjust the required pH, and then add a certain amount of DMC, the concentration of alkali lignin is 2.5 g / L, alkali lignin:DMC ratio is 1:7, heated in water bath to the required temperature of 40°C, stirred with magnetic stirrer (rotating speed 200 r / min), inserted cathode and anode electrodes (the effective area of anode and cathode is 3.5 cm×4 cm, the distance between the two electrodes is 5 cm), turn on the power button, adjust the voltage to 3.5v, let the lignin graft copolymerization reaction start, the reaction time is 4h, after the reaction, the sample is in ethanol with a mass fraction ≥75% Precipitate in the medium, let it stand for enough time, after the precipitation is completely settled, pour off the supernatant, leave the precipitation, wash the copolymer twice with ethanol with a m...
Embodiment 3
[0044]The preparation method of lignin-DMC graft copolymer: add a certain amount of alkali lignin in the electrolytic cell, add an appropriate amount of deionized water to dissolve, adjust the required pH, and then add a certain amount of DMC, the concentration of alkali lignin is 7.5 g / L, alkali lignin: DMC ratio of 1:5, heated in a water bath to the required temperature of 70°C, stirred with a magnetic stirrer (rotating speed 200 r / min), inserted the cathode and anode electrodes (the effective area of the anode and cathode were 3.5 cm×4 cm, the distance between the two electrodes is 5 cm), turn on the power button, adjust the voltage to 5.5v, let the lignin graft copolymerization reaction start, the reaction time is 3h, after the reaction, the sample is in ethanol with a mass fraction ≥75% Precipitate in the medium, let it stand for enough time, after the precipitation is completely settled, pour off the supernatant, leave the precipitation, wash the copolymer twice with et...
PUM
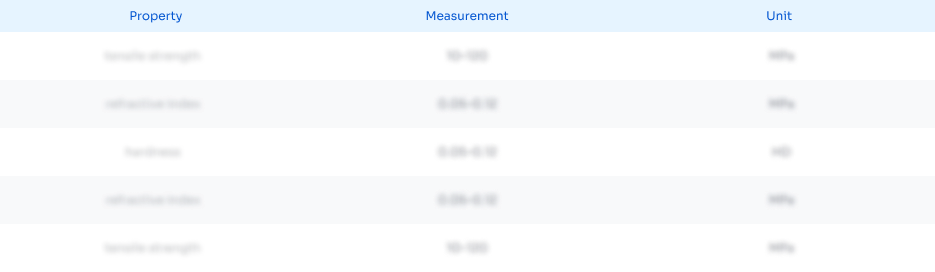
Abstract
Description
Claims
Application Information

- R&D
- Intellectual Property
- Life Sciences
- Materials
- Tech Scout
- Unparalleled Data Quality
- Higher Quality Content
- 60% Fewer Hallucinations
Browse by: Latest US Patents, China's latest patents, Technical Efficacy Thesaurus, Application Domain, Technology Topic, Popular Technical Reports.
© 2025 PatSnap. All rights reserved.Legal|Privacy policy|Modern Slavery Act Transparency Statement|Sitemap|About US| Contact US: help@patsnap.com