A 3D printing last forming method
A molding method and 3D printing technology, applied in the direction of additive processing, processing and manufacturing, etc., to achieve the effect of accurate upper surface, lower development cost and simple operation
- Summary
- Abstract
- Description
- Claims
- Application Information
AI Technical Summary
Problems solved by technology
Method used
Image
Examples
Embodiment Construction
[0028] The present invention will be described in further detail below in conjunction with the embodiments given in the accompanying drawings.
[0029] refer to Figure 1 to Figure 3 As shown, a 3D printing last forming method of this embodiment includes
[0030] Step 1, download the required shoe last model, modify the data of the shoe last model with drawing software and convert the data of the shoe last model into the format required by the 3D printer;
[0031] Step 2, output the shoe last data to the 3D printer and print out the required shoe last;
[0032] Step 3, select the midsole and heat insulation film of the corresponding size, put the heat insulation film on the shoe last and nail the midsole to the bottom of the shoe last;
[0033] Step 4, put the upper into the last, and use nails to fix the upper on the last and the midsole;
[0034] Step five, use a hammer to smooth the upper, then use glue to bond the midsole and the upper of the upper, and then pull out th...
PUM
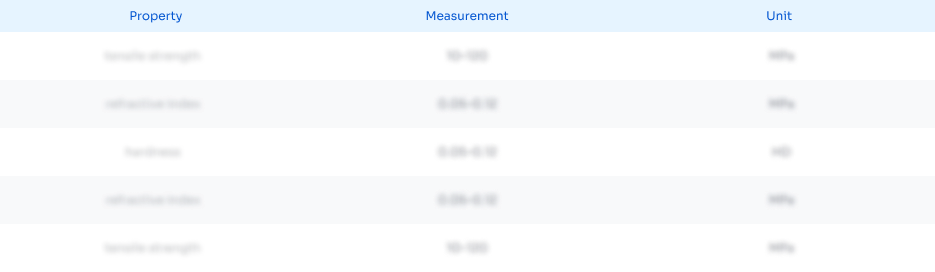
Abstract
Description
Claims
Application Information

- R&D
- Intellectual Property
- Life Sciences
- Materials
- Tech Scout
- Unparalleled Data Quality
- Higher Quality Content
- 60% Fewer Hallucinations
Browse by: Latest US Patents, China's latest patents, Technical Efficacy Thesaurus, Application Domain, Technology Topic, Popular Technical Reports.
© 2025 PatSnap. All rights reserved.Legal|Privacy policy|Modern Slavery Act Transparency Statement|Sitemap|About US| Contact US: help@patsnap.com