A method for improving sinter yield in converter smelting
A converter smelting and sintering technology, which is applied in the manufacture of converters, etc., can solve the problems of silo damage, cost increase, and high processing costs, and achieve the effects of increasing service life, reducing maintenance costs, and increasing yield
- Summary
- Abstract
- Description
- Claims
- Application Information
AI Technical Summary
Problems solved by technology
Method used
Examples
Embodiment Construction
[0023] A method for improving sinter yield in converter smelting according to the present invention is characterized in that it comprises the following steps:
[0024] 1) Raw material handling;
[0025] a) On the basis of meeting the clearance requirements of the molten iron tank, the amount of mixed iron is controlled at more than 90%, and all the molten iron in front of the furnace is fully mixed;
[0026] b) Conditions of molten iron: 0.30% ≤ silicon content of molten iron ≤ 0.60%, the temperature of molten iron entering the furnace is greater than 1260°C;
[0027] 2) Requirements for converter operation:
[0028] a) After the conversion of iron into the converter is completed, shake the converter to the zero position. According to the temperature of the molten iron and the silicon content of the molten iron, the total amount of sinter added is controlled at 8-12 tons / furnace, and added at one time:
[0029] b) After the sinter is added, when the bottom-blowing converter ...
PUM
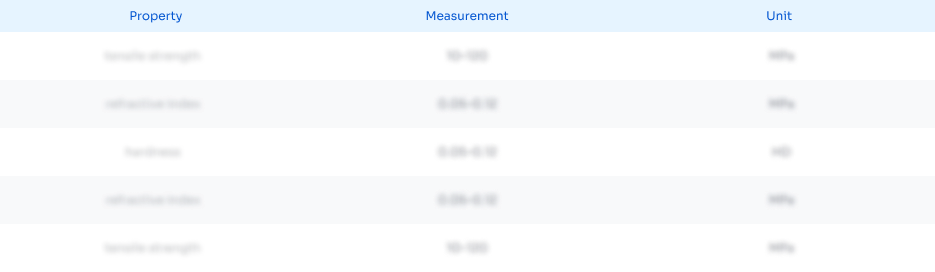
Abstract
Description
Claims
Application Information

- R&D
- Intellectual Property
- Life Sciences
- Materials
- Tech Scout
- Unparalleled Data Quality
- Higher Quality Content
- 60% Fewer Hallucinations
Browse by: Latest US Patents, China's latest patents, Technical Efficacy Thesaurus, Application Domain, Technology Topic, Popular Technical Reports.
© 2025 PatSnap. All rights reserved.Legal|Privacy policy|Modern Slavery Act Transparency Statement|Sitemap|About US| Contact US: help@patsnap.com