A kind of molding method of automobile seat headrest
A molding method and technology for car seats, which are applied to household appliances, other household appliances, household components, etc., can solve the problems of heavy production cost burden, large amount of engineering, cumbersome processes, etc., and achieve less defective molding, low cost, and improved The effect of product qualification rate
- Summary
- Abstract
- Description
- Claims
- Application Information
AI Technical Summary
Problems solved by technology
Method used
Examples
Embodiment Construction
[0021] The present invention will be specifically introduced below in conjunction with specific embodiments.
[0022] A molding method for a car seat headrest, characterized in that it comprises the following process steps:
[0023] S0. Fabric preparation: sewing or embroidering patterns, characters or trademarks on any position of the fabric;
[0024] S1, coating: a layer of film is bonded on the base sponge to obtain the first complex; on the film of the first complex, the outer sponge is bonded to obtain the second complex; the base sponge of the second complex is Composite bonding with the fabric to obtain a finished composite fabric; wherein, the film is made of polytetrafluoroethylene material, the base layer sponge and the outer layer sponge are made of foamed sponge material, between the base layer sponge and the film, the film Both the outer sponge and the base sponge and the fabric are bonded together by flame compounding;
[0025] S2, cutting: place the finished c...
PUM
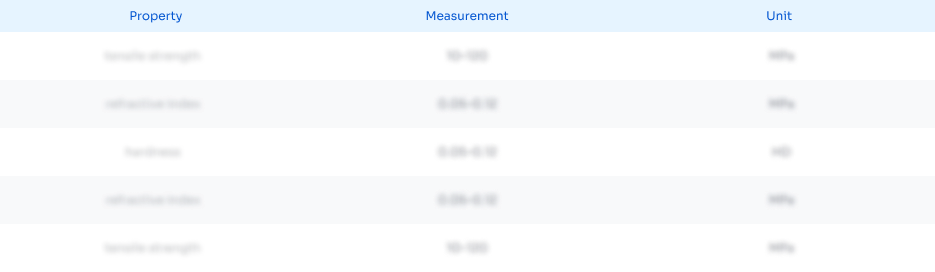
Abstract
Description
Claims
Application Information

- R&D Engineer
- R&D Manager
- IP Professional
- Industry Leading Data Capabilities
- Powerful AI technology
- Patent DNA Extraction
Browse by: Latest US Patents, China's latest patents, Technical Efficacy Thesaurus, Application Domain, Technology Topic, Popular Technical Reports.
© 2024 PatSnap. All rights reserved.Legal|Privacy policy|Modern Slavery Act Transparency Statement|Sitemap|About US| Contact US: help@patsnap.com