Impeller production clamp for passenger car turbocharger
A turbocharger and passenger car technology, applied in clamping, manufacturing tools, supports, etc., can solve the problems of low pass rate of processing, difficulty in guaranteeing impeller parts, heavy inspection workload, etc., and achieve product quality The effect of stability, saving auxiliary time, and convenient operation
- Summary
- Abstract
- Description
- Claims
- Application Information
AI Technical Summary
Problems solved by technology
Method used
Image
Examples
Embodiment Construction
[0024] like Figure 2-4 As shown, the impeller production jig of a passenger car turbocharger includes a linear optical axis 6 and a linear bearing 5 sleeved on the front end of the linear optical axis 6. On the linear optical axis 6, the rear end of the linear bearing 5 is also A compression spring 7 and a retaining ring 8 are provided, and a boss 5.1 is provided on the front end of the linear bearing 5, and a flange 3 is sleeved outside the linear bearing 5 and clamped at the boss 5.1 , the boss 5.1 also supports an A reference plane positioning plate 1 at the front end of the linear optical axis 6 and perpendicular to the axial direction of the linear optical axis 6 through the bracket 4, and the A reference plane positioning plate 1 is provided with a through hole, A circle of steps matching the structure of the A reference plane of the part 2 is provided around the through hole, and a tapered positioning hole 6.1 is also provided at the front end of the linear optical axi...
PUM
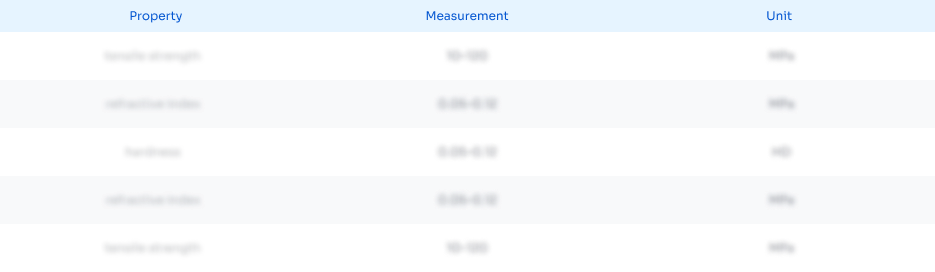
Abstract
Description
Claims
Application Information

- R&D
- Intellectual Property
- Life Sciences
- Materials
- Tech Scout
- Unparalleled Data Quality
- Higher Quality Content
- 60% Fewer Hallucinations
Browse by: Latest US Patents, China's latest patents, Technical Efficacy Thesaurus, Application Domain, Technology Topic, Popular Technical Reports.
© 2025 PatSnap. All rights reserved.Legal|Privacy policy|Modern Slavery Act Transparency Statement|Sitemap|About US| Contact US: help@patsnap.com