Post-casting system for fabricated shear wall without template
A shear wall and prefabricated technology, which is applied in the direction of construction and building construction, can solve the problems of inability to directly install vertically and low assembly efficiency, and achieve the goal of avoiding overlapping and inability to install vertically, improving assembly efficiency, and ensuring safety Effect
- Summary
- Abstract
- Description
- Claims
- Application Information
AI Technical Summary
Problems solved by technology
Method used
Image
Examples
Embodiment 1
[0033] Such as figure 1 and figure 2 Commonly shown, a post-casting system for prefabricated shear walls without formwork, including a first shear wall 1 and a second shear wall 2, the end surface of the first shear wall 1 is provided with a vertical groove 11, so A plurality of stirrups 12 are arranged at vertical intervals in the vertical groove 11, preferably, the stirrups 12 are closed stirrups, and a plurality of insertion vertical grooves are arranged at vertical intervals on the second shear wall 2 The flexible connecting piece 21 inside the vertical groove 11 is poured with concrete, and the concrete connects the first shear wall 1 and the second shear wall 2 together.
[0034] The rear inserted reinforcement bar assembly 3 is arranged in the vertical groove 11 . In this way, before the concrete is poured in the vertical groove 11, the rear-inserted steel bar assembly 3 is directly inserted into the vertical groove 11, which saves the existing step of binding steel ...
Embodiment 2
[0040] This embodiment is basically the same as Embodiment 1, the difference is that, as image 3 and Figure 4 Commonly shown, there are two rows of flexible connectors 21, and the two rows of flexible connectors 21 are symmetrically arranged on both sides of the second shear wall 2. Correspondingly, there are two first shear walls 1 and two first shear walls. The wall 1 is arranged symmetrically on both sides of the second shear wall 2, and the concrete connects the two first shear walls 1 and the second shear wall 2 to form a cross-shaped node.
[0041] In this embodiment, the middle part of each flexible connecting piece 21 is arranged in the second shear wall 2 , and its two ends extend out of the second shear wall 2 respectively.
Embodiment 3
[0043] This embodiment is basically the same as Embodiment 1, the difference is that, as Figure 5 and Figure 6 As shown together, the flexible connector 21 is arranged on one side of the second shear wall 2 and is arranged close to the end face of the second shear wall 2, and the concrete connects the first shear wall 1 and the second shear wall 2 to form a L-shaped nodes.
PUM
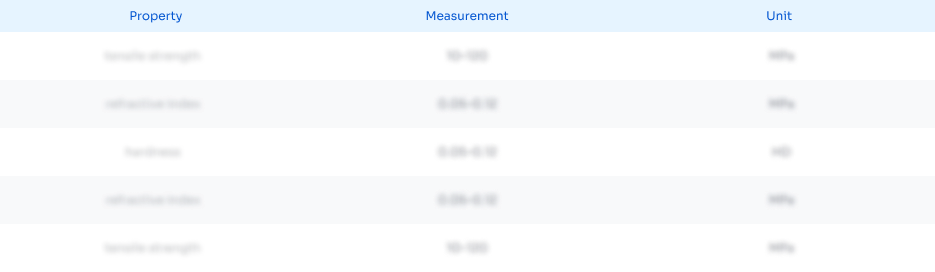
Abstract
Description
Claims
Application Information

- Generate Ideas
- Intellectual Property
- Life Sciences
- Materials
- Tech Scout
- Unparalleled Data Quality
- Higher Quality Content
- 60% Fewer Hallucinations
Browse by: Latest US Patents, China's latest patents, Technical Efficacy Thesaurus, Application Domain, Technology Topic, Popular Technical Reports.
© 2025 PatSnap. All rights reserved.Legal|Privacy policy|Modern Slavery Act Transparency Statement|Sitemap|About US| Contact US: help@patsnap.com