Electric thread sleeve used for steel bar connection and screwing device
A threaded sleeve and electric technology, applied in the processing of building materials, structural elements, building components, etc., can solve the problems of small rotation range and low efficiency of the wrench, and achieve the effect of good meshing performance, stable transmission and reduced impact.
- Summary
- Abstract
- Description
- Claims
- Application Information
AI Technical Summary
Problems solved by technology
Method used
Image
Examples
Embodiment 1
[0020] A tightener and an electric threaded sleeve, the structure of which is as follows Figure 1 ~ Figure 3 As shown, the details are as follows: it includes a rotating motor, a driving gear 1 arranged on the main shaft of the rotating motor, and is arranged between the driving gear 1 and the outer wall of the electric threaded sleeve 4 and meshes with the teeth of the driving gear 1 and the electric threaded sleeve 4 gear set. Wherein, the gear set includes two No. 1 gear sets 2 symmetrically meshed on both sides of the driving gear, and No. 2 gear sets 3 arranged between each No. 1 gear set 1 and the outer wall 4 of the electric threaded sleeve. The No. 1 gear set No. 2 and No. 2 gear sets 3 both include a bull gear and a pinion coaxially arranged with the bull gear and rotating synchronously. The bull gear 21 of the No. 1 gear set meshes with the driving gear 1, and the pinion 22 of the No. 1 gear set meshes with the second gear. The bull gear 31 engagement of No. 2 gear...
PUM
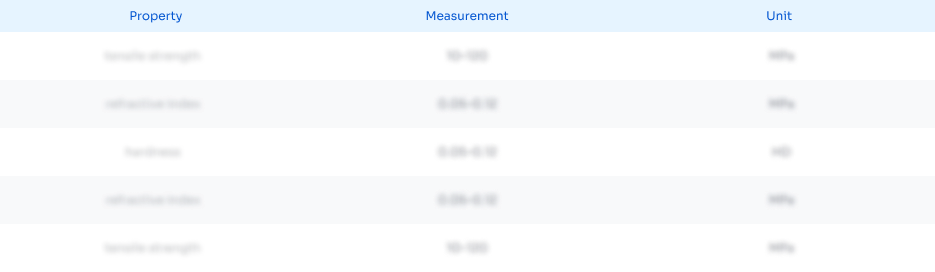
Abstract
Description
Claims
Application Information

- R&D Engineer
- R&D Manager
- IP Professional
- Industry Leading Data Capabilities
- Powerful AI technology
- Patent DNA Extraction
Browse by: Latest US Patents, China's latest patents, Technical Efficacy Thesaurus, Application Domain, Technology Topic, Popular Technical Reports.
© 2024 PatSnap. All rights reserved.Legal|Privacy policy|Modern Slavery Act Transparency Statement|Sitemap|About US| Contact US: help@patsnap.com