A method for preparing α-o-nitrophenylethanol by oxidation of o-nitroethylbenzene with catalyst-free oxygen
A technology of o-nitroethylbenzene and nitroethylbenzene, which is applied in the field of catalyst-free oxygen oxidation of o-nitroethylbenzene to prepare α-o-nitrophenylethanol, which can solve the difficulty of catalyst synthesis and the selection of α-o-nitrophenylethanol low yield, low conversion rate and yield, etc., to achieve the effect of cheap recycling, easy recycling and moderate reaction temperature
- Summary
- Abstract
- Description
- Claims
- Application Information
AI Technical Summary
Problems solved by technology
Method used
Image
Examples
Embodiment 1
[0024] Get o-nitroethylbenzene (907mg, 6mmol), sodium hydroxide (1.8g, 45mmol), add in 100ml autoclave, add methanol 10ml; After filling and changing oxygen three times, feed oxygen (pressure 1.8MPa), in oil bath The reaction was carried out at a temperature of 65° C. for 24 hours. After the reaction, add methanol for dilution, neutralize the pH value of the reaction mixture to 2-3, remove most of the solvent under reduced pressure, add ethyl acetate, dry and filter. After chromatographic column separation, 45 mg (0.30 mmol) of o-nitroethylbenzene was recovered, and the conversion rate of o-nitroethylbenzene was 95%, and 522 mg (3.12 mmol) of α-o-nitrophenylethanol was obtained, with a yield of 52%.
Embodiment 2
[0026] Get o-nitroethylbenzene (907mg, 6mmol), sodium hydroxide (1.8g, 45mmol), add in 100ml autoclave, add methanol 10ml; After filling and changing oxygen three times, feed oxygen (pressure 1.8MPa), in oil bath The reaction was carried out at a temperature of 65° C. for 24 hours. After the reaction, add methanol for dilution, neutralize the pH value of the reaction mixture to 4-5, remove most of the solvent under reduced pressure, add ethyl acetate, dry and filter. After chromatographic column separation, 27mg (0.18mmol) of o-nitroethylbenzene was recovered, and the conversion rate of o-nitroethylbenzene was 97%, and 702mg (4.20mmol) of α-o-nitrophenylethanol was obtained, with a yield of 70%.
Embodiment 3
[0028] Get o-nitroethylbenzene (907mg, 6mmol), sodium hydroxide (1.8g, 45mmol), add in 100ml autoclave, add methanol 10ml; After filling and changing oxygen three times, feed oxygen (pressure 1.8MPa), in oil bath The reaction was carried out at a temperature of 65° C. for 24 hours. After the reaction, add methanol for dilution, neutralize the pH value of the reaction mixture to 6-7, remove most of the solvent under reduced pressure, add ethyl acetate, dry and filter. After chromatographic column separation, 27.2mg (0.18mmol) of o-nitroethylbenzene was recovered, and the conversion rate of o-nitroethylbenzene was 97%, and 632mg (3.78mmol) of α-o-nitrophenylethanol was obtained, with a yield of 63%.
PUM
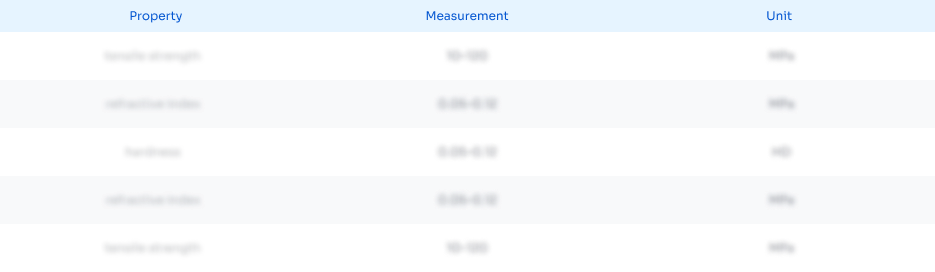
Abstract
Description
Claims
Application Information

- Generate Ideas
- Intellectual Property
- Life Sciences
- Materials
- Tech Scout
- Unparalleled Data Quality
- Higher Quality Content
- 60% Fewer Hallucinations
Browse by: Latest US Patents, China's latest patents, Technical Efficacy Thesaurus, Application Domain, Technology Topic, Popular Technical Reports.
© 2025 PatSnap. All rights reserved.Legal|Privacy policy|Modern Slavery Act Transparency Statement|Sitemap|About US| Contact US: help@patsnap.com