Method for Predicting Mechanical Response Characteristics of Consolidated Filling Body Based on Sensitive Microscopic Parameters
A cemented filling, mechanical response technology, applied in special data processing applications, electrical digital data processing, instruments, etc., can solve the problems of delayed mining construction period, long test period, and inability to determine the primary and secondary relationship of microscopic parameters.
- Summary
- Abstract
- Description
- Claims
- Application Information
AI Technical Summary
Problems solved by technology
Method used
Image
Examples
Embodiment Construction
[0124] Such as figure 1 As shown, the method for predicting the mechanical response characteristics of cemented filling body based on sensitive microscopic parameters of the present invention includes the following steps:
[0125] Step 1. Determine the sensitive microscopic parameters of the cemented filling body that are sensitive to the mechanical response characteristics;
[0126] In this embodiment, the specific process of determining the sensitive micro-parameters of the cemented filling body sensitive to the mechanical response characteristics described in step 1 is as follows:
[0127] Step 101, take a part from each of the multiple cemented filling body samples 19 of different curing ages to make a SEM scanning electron microscope sample, and the remaining part is used as a triaxial compressive strength test sample; and multiple SEM scanning electron microscope samples and multiple Triaxial compressive strength test samples are numbered one by one according to the cur...
PUM
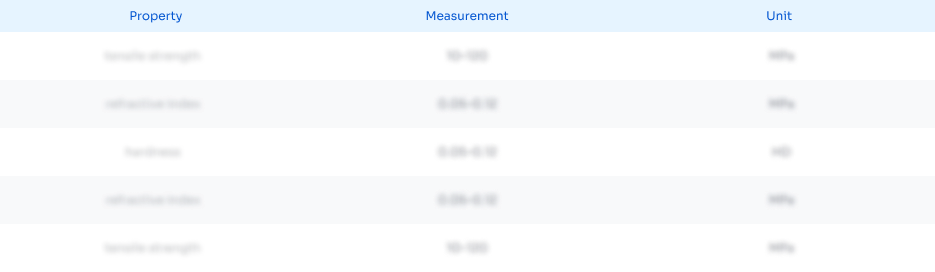
Abstract
Description
Claims
Application Information

- R&D
- Intellectual Property
- Life Sciences
- Materials
- Tech Scout
- Unparalleled Data Quality
- Higher Quality Content
- 60% Fewer Hallucinations
Browse by: Latest US Patents, China's latest patents, Technical Efficacy Thesaurus, Application Domain, Technology Topic, Popular Technical Reports.
© 2025 PatSnap. All rights reserved.Legal|Privacy policy|Modern Slavery Act Transparency Statement|Sitemap|About US| Contact US: help@patsnap.com