Preparation method of flame-retarding type polyurethane synthetic leather
A polyurethane and synthetic leather technology, applied in polyurea/polyurethane coatings, coatings, textiles and papermaking, etc., can solve the problems of non-flammability, unsatisfactory, poor strength, etc., to enhance the steric hindrance effect, reduce Surface polarity, effect of lowering surface temperature
- Summary
- Abstract
- Description
- Claims
- Application Information
AI Technical Summary
Problems solved by technology
Method used
Image
Examples
example 1
[0022]Weigh 16g of sodium hydroxide and 10g of anhydrous sodium carbonate, mix them in a beaker with 100mL of deionized water, and stir for 8 minutes to obtain a mixed alkali solution, and then mix magnesium chloride hexahydrate, trihydrate hexahydrate with a mass ratio of 3:1:6 Aluminum chloride and deionized water were mixed and stirred for 12 minutes to obtain a self-made salt solution, and 55 mL of a self-made salt solution and 30 mL of a mixed alkali solution were measured respectively for later use, and the pH of the self-made salt solution was adjusted to 10 with a mixed alkali solution to obtain a suspension; Put the turbid liquid at room temperature and let it age for 2 hours, remove the filtrate by filtration, take out the filter residue, wash the filter residue 3 times with deionized water, put the washed filter residue in an oven, dry at 85°C for 1 hour, and grind out To obtain self-made magnesium-aluminum hydrotalcite powder, mix self-made magnesium-aluminum hydrot...
example 2
[0024] Weigh 18g of sodium hydroxide and 11g of anhydrous sodium carbonate, mix them in a beaker with 110mL of deionized water and stir for 9 minutes to obtain a mixed alkali solution, and then mix magnesium chloride hexahydrate, trihydrate hexahydrate with a mass ratio of 3:1:6 Aluminum chloride and deionized water were mixed and stirred for 14 minutes to obtain a self-made salt solution, and 60 mL of a self-made salt solution and 37 mL of a mixed alkali solution were measured for subsequent use, and the pH of the self-made salt solution was adjusted to 11 with a mixed alkali solution to obtain a suspension; Put the turbid liquid at room temperature for 3 hours, filter to remove the filtrate, take out the filter residue, wash the filter residue 4 times with deionized water, put the washed filter residue in an oven, dry at 90°C for 1.5h, and grind Discharge to obtain self-made magnesium aluminum hydrotalcite powder, mix self-made magnesium aluminum hydrotalcite powder and sodiu...
example 3
[0026] Weigh 20g of sodium hydroxide and 12g of anhydrous sodium carbonate, mix them in a beaker with 120mL of deionized water and stir for 10min to obtain a mixed alkali solution, and then mix magnesium chloride hexahydrate, trihydrate hexahydrate with a mass ratio of 3:1:6 Aluminum chloride and deionized water were mixed and stirred for 16 minutes to obtain a self-made salt solution, and 65 mL of a self-made salt solution and 45 mL of a mixed alkali solution were measured for subsequent use, and the pH of the self-made salt solution was adjusted to 12 with a mixed alkali solution to obtain a suspension; Put the turbid liquid at room temperature and let it age for 4 hours, remove the filtrate by filtration, take out the filter residue, wash the filter residue 5 times with deionized water, put the washed filter residue in an oven, dry at 95°C for 2 hours, and grind out To obtain self-made magnesium-aluminum hydrotalcite powder, mix self-made magnesium-aluminum hydrotalcite powd...
PUM
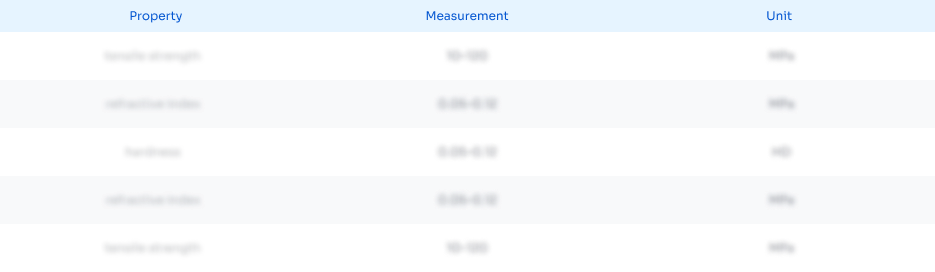
Abstract
Description
Claims
Application Information

- R&D
- Intellectual Property
- Life Sciences
- Materials
- Tech Scout
- Unparalleled Data Quality
- Higher Quality Content
- 60% Fewer Hallucinations
Browse by: Latest US Patents, China's latest patents, Technical Efficacy Thesaurus, Application Domain, Technology Topic, Popular Technical Reports.
© 2025 PatSnap. All rights reserved.Legal|Privacy policy|Modern Slavery Act Transparency Statement|Sitemap|About US| Contact US: help@patsnap.com