Repairing method for refractory material layer of rotary kiln
A technology of refractory material and rotary kiln, applied in the field of rotary kiln, can solve the problems of small area shedding of refractory material layer, damage to the body of the rotary kiln, affecting the production of pellets, etc., so as to achieve the effect of improving the service life and improving the repair effect.
- Summary
- Abstract
- Description
- Claims
- Application Information
AI Technical Summary
Problems solved by technology
Method used
Examples
Embodiment 1
[0012] When the rotary kiln is not turned off and production is stopped, reduce the temperature inside the rotary kiln body to 400°C, and directly repair the refractory material layer to be repaired by the slurry gunning machine. The repaired area is 0.1 square meters and it takes 15 minutes.
Embodiment 2
[0014] When the rotary kiln is not turned off and production is stopped, reduce the temperature inside the rotary kiln body to 420°C, and directly repair the refractory material layer to be repaired by the slurry gunning machine. The repaired area is 0.15 square meters and it takes 20 minutes.
Embodiment 3
[0016] When the rotary kiln is not turned off and production is stopped, reduce the temperature inside the rotary kiln body to 450°C, and directly repair the refractory material layer to be repaired by the slurry gunning machine. The repaired area is 0.2 square meters and it takes 24 minutes.
PUM
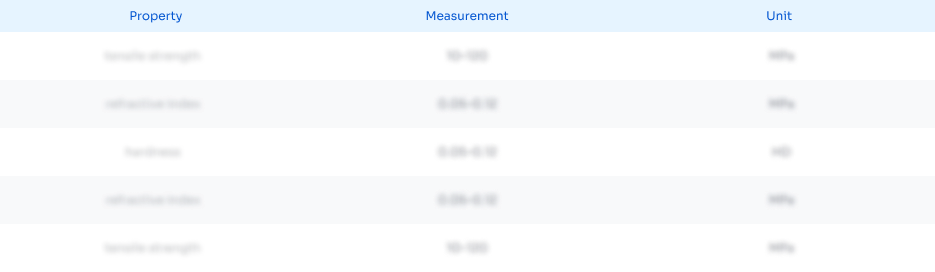
Abstract
Description
Claims
Application Information

- Generate Ideas
- Intellectual Property
- Life Sciences
- Materials
- Tech Scout
- Unparalleled Data Quality
- Higher Quality Content
- 60% Fewer Hallucinations
Browse by: Latest US Patents, China's latest patents, Technical Efficacy Thesaurus, Application Domain, Technology Topic, Popular Technical Reports.
© 2025 PatSnap. All rights reserved.Legal|Privacy policy|Modern Slavery Act Transparency Statement|Sitemap|About US| Contact US: help@patsnap.com