Lead zinc ore beneficiation process capable of saving clean water
A process method, the technology of lead-zinc ore, applied in flotation, solid separation, etc., can solve the problems of wasting water resources, low recycling rate of mine production water, and affecting the ecological environment, so as to reduce the consumption of clean water and save clean water The effect of consumption and improvement of beneficiation indicators
- Summary
- Abstract
- Description
- Claims
- Application Information
AI Technical Summary
Problems solved by technology
Method used
Image
Examples
Embodiment 1
[0019] The properties of the ore in Example 1 are: lead-zinc ore raw ore multi-element content: Pb3.2%, Zn5.8%, S29%, Ag 125g / t. Oxidation rate of ore: Pb5.52%, Zn4.85%.
[0020] The technical process conditions of Example 1 are: Lead selection: Grinding fineness -200 mesh (-0.074mm) is 75%; lead selection roughing initial concentration is 35%, pulp pH 10.5, pharmaceutical system: aniline 30g / t , sulfur nitrogen 15 g / t, zinc sulfate 1000 g / t, sodium sulfite 600 g / t; zinc selection: copper sulfate 400 g / t, lime 3000 g / t, butyl xanthate 250 g / t; sulfur selection: add Sulfuric acid is used to adjust the pH to 7-7.5, and butyl xanthate is 750 g / t. The amount of foaming agent (using terpineol oil) is added as needed. Mineral processing process see figure 2 , image 3 . The closed-circuit results of the laboratory are shown in Table 1.
[0021] Table 1: Comparative results of test index of embodiment 1
[0022]
[0023] It can be seen from Table 1 that the image 3 The be...
Embodiment 2
[0025] The ore properties and mineral composition of Example 2 are the same as those in Example 1. The technical process conditions of Example 2 are: lead selection: grinding fineness-200 mesh (-0.074mm) is 75%; pulp concentration is 35%, and the pulp pH 10.5, chemical system: aniline 30g / t, sulfur nitrogen 15 g / t, zinc sulfate 1000 g / t, sodium sulfite 600 g / t; zinc selection: copper sulfate 400 g / t, lime 3000 g / t, butyl Xanthate 250 g / t; sulfur selection: add sulfuric acid to adjust pH to 7-7.5, butyl xanthate 750 g / t; foaming agent (terpineol oil) is added as needed. Mineral processing process see figure 1 , image 3 . The closed-circuit results of the laboratory are shown in Table 2.
[0026] Table 2: Comparative results of test index of embodiment 2
[0027]
[0028] It can be seen from Table 2 that the figure 1 The beneficiation process is compared with image 3 process, under the same reagent conditions, the remaining reclaimed water from various concentrates an...
Embodiment 3
[0030] The ore properties and mineral composition of Example 3 are the same as those in Example 1. The technical process conditions of Example 3 are: lead selection: grinding fineness-200 mesh (-0.074mm) is 75%; the pulp concentration is 35%, and the pulp pH 10.5, chemical system: aniline 30g / t, sulfur nitrogen 15 g / t, zinc sulfate 1000 g / t, sodium sulfite 600 g / t; zinc selection: copper sulfate 400 g / t, lime 3000 g / t, butyl Xanthate 250 g / t; sulfur selection: add sulfuric acid to adjust pH to 7-7.5, butyl xanthate 750 g / t; foaming agent (terpineol oil) is added as needed. Mineral processing process see figure 1 , Figure 4 . The closed-circuit results of the laboratory are shown in Table 3.
[0031] Table 3: Comparative results of test index in embodiment 3
[0032]
[0033] It can be seen from Table 3 that the Figure 4 The beneficiation process is compared with figure 1 process, under the same chemical conditions, the water from various concentrates and tailings in...
PUM
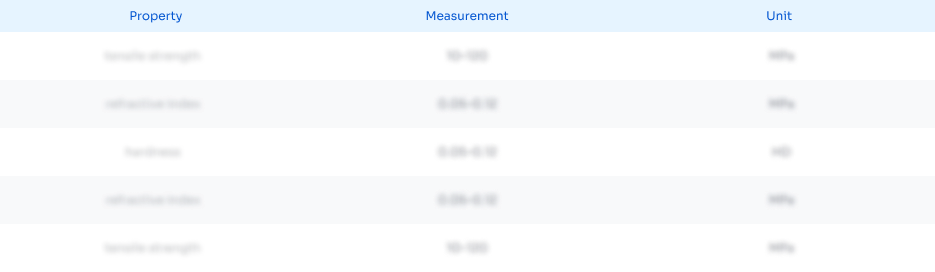
Abstract
Description
Claims
Application Information

- R&D
- Intellectual Property
- Life Sciences
- Materials
- Tech Scout
- Unparalleled Data Quality
- Higher Quality Content
- 60% Fewer Hallucinations
Browse by: Latest US Patents, China's latest patents, Technical Efficacy Thesaurus, Application Domain, Technology Topic, Popular Technical Reports.
© 2025 PatSnap. All rights reserved.Legal|Privacy policy|Modern Slavery Act Transparency Statement|Sitemap|About US| Contact US: help@patsnap.com