A Split-free Substructure Frequency Response Function Identification Method
A frequency response function and mechanical system technology, which is applied in the field of mechanical vibration analysis and detection, can solve problems such as the frequency response function between degrees of freedom that cannot be calculated, and achieve improved operability and analysis efficiency, strong engineering applicability, and improved analysis efficiency Effect
- Summary
- Abstract
- Description
- Claims
- Application Information
AI Technical Summary
Problems solved by technology
Method used
Image
Examples
Embodiment 1
[0026] Such as figure 1 As shown, this embodiment includes the following steps:
[0027] Step one, to figure 2 The discrete mechanical system shown includes active parts and passive parts, and the active part consists of four mass blocks M 5 , M 6 , M 8 , M 9 Composition, the passive part consists of 5 mass blocks M 1 ~ M 4 , M 7 Composition, there are 3 transmission paths K between the active part and the passive part 35 、K 46 、K 78 , the mass M 3 , M 4 and M 7 is the coupling point on the passive side, and the mass M 5 , M 6 , M 8 is the coupling point on the side of the active part, and the mass M 1 The displacement is the target response, there are 7 measurement points in total, and the analysis frequency range is 1-250Hz.
[0028] Step 2. Measure the frequency response function of the coupling mechanical system: measure the frequency response function matrix H of the active part of the coupling point c,aa , The frequency response function matrix H of th...
Embodiment 2
[0033] Such as Figure 4 As shown, the present embodiment has shown the simple physical model of vehicle body, and this model comprises vehicle body (passive parts, such as Figure 4 (a) shown) and "engine" bracket (active parts, such as Figure 4 As shown in (c), the bracket is connected to the vehicle body through three rubber suspensions. The experimental device is as follows Figure 4 (b) shown.
[0034] This embodiment includes the following steps:
[0035] Step 1. Determine the measurement point and analyze the frequency range: record the suspension points on the side of the active part as a1, a2 and a3, and the suspension points on the side of the passive part as p1, p2 and p3. The schematic diagram of the suspension and the global coordinate system are as follows: Figure 5 shown. The target point is a point (one-way) vibration response on the right side of the vehicle body, denoted as t. Only the translational degrees of freedom of the suspension points are consi...
PUM
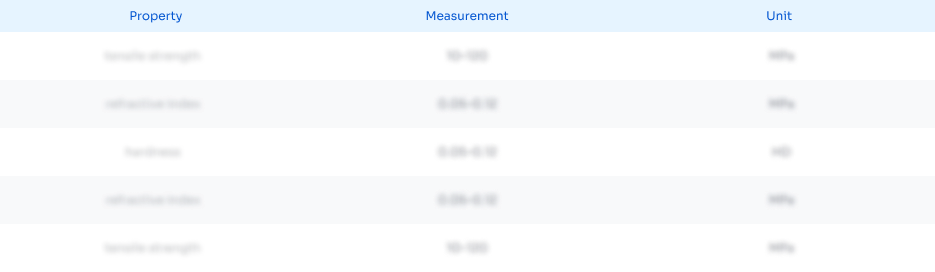
Abstract
Description
Claims
Application Information

- Generate Ideas
- Intellectual Property
- Life Sciences
- Materials
- Tech Scout
- Unparalleled Data Quality
- Higher Quality Content
- 60% Fewer Hallucinations
Browse by: Latest US Patents, China's latest patents, Technical Efficacy Thesaurus, Application Domain, Technology Topic, Popular Technical Reports.
© 2025 PatSnap. All rights reserved.Legal|Privacy policy|Modern Slavery Act Transparency Statement|Sitemap|About US| Contact US: help@patsnap.com