Method for predicting residual stress of metal plate based on residual stress release warpage
A residual stress and metal plate technology, applied in force/torque/work measuring instruments, measuring devices, instruments, etc., can solve the problems of harsh test environment, unsuitable control of aluminum alloy properties, and expensive residual stress test equipment. , to achieve the effect of high measurement efficiency and simple operation
- Summary
- Abstract
- Description
- Claims
- Application Information
AI Technical Summary
Problems solved by technology
Method used
Image
Examples
Embodiment Construction
[0020] Below in conjunction with accompanying drawing and specific embodiment the present invention will be described in further detail:
[0021] (1) Use one of the methods of X-ray method, blind hole method, ultrasonic method, crack flexibility method or finite element analysis method to measure the residual stress of aluminum alloy plates with different thicknesses. The residual stress distribution of aluminum alloy thick plates is as follows figure 2 shown.
[0022] (2) Fix one end of the aluminum alloy thick plate, such as figure 1 For the section line part, the length of the fixed part is less than 1 / 2 of the length of the sample, and then place a displacement sensor such as a dial indicator or a laser sensor at point a in the center of the edge of one end of the plate 1, and record the initial value. At 2 places, wire cutting is performed along the plate thickness with wire cutting wire 2. Schematic diagram of warping displacement according to different wire cutting d...
PUM
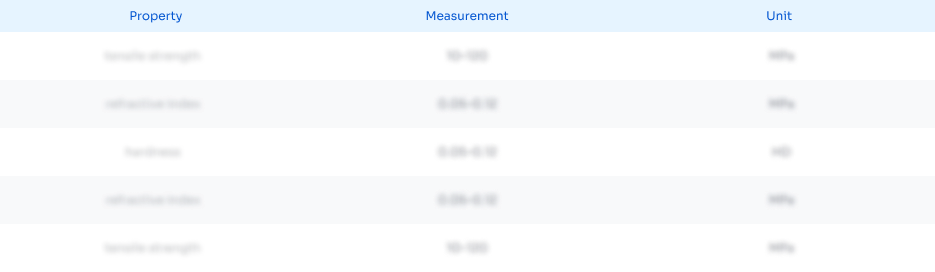
Abstract
Description
Claims
Application Information

- R&D
- Intellectual Property
- Life Sciences
- Materials
- Tech Scout
- Unparalleled Data Quality
- Higher Quality Content
- 60% Fewer Hallucinations
Browse by: Latest US Patents, China's latest patents, Technical Efficacy Thesaurus, Application Domain, Technology Topic, Popular Technical Reports.
© 2025 PatSnap. All rights reserved.Legal|Privacy policy|Modern Slavery Act Transparency Statement|Sitemap|About US| Contact US: help@patsnap.com