Force-feedback teleoperation main hand
A technology of teleoperation and force feedback, applied in the directions of manipulators, program-controlled manipulators, manufacturing tools, etc., can solve the problem of not being able to use the control joint to rotate, and achieve the effects of compact structure, improved comfort, and reduced fatigue.
- Summary
- Abstract
- Description
- Claims
- Application Information
AI Technical Summary
Problems solved by technology
Method used
Image
Examples
Embodiment Construction
[0037] The main hand of force feedback remote operation of the present invention, such as figure 1 As shown, it includes a first link part 1 , a second link part 2 , a third link part 3 , a fourth link part 4 , a fifth link part 5 and a knob part 6 connected in sequence. Each connecting rod part is connected by a rotary joint, and a potentiometer or an encoder is installed on each rotary joint, wherein the first connecting rod part 1, the second connecting rod part 2 and the third connecting rod part 3 A motor and a reducer are installed on the rotary joint at the connection, the motor in the first link part is connected to the input end of the reducer, and the motors in the second link part and the third link part are connected to the reducer through a synchronous belt transmission , for deceleration transmission, the angular displacement of the output end is measured by the corresponding potentiometer through a pair of gear transmission.
[0038] The structure of the first ...
PUM
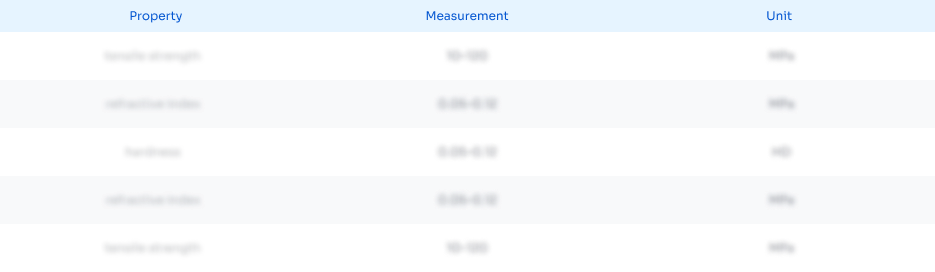
Abstract
Description
Claims
Application Information

- R&D Engineer
- R&D Manager
- IP Professional
- Industry Leading Data Capabilities
- Powerful AI technology
- Patent DNA Extraction
Browse by: Latest US Patents, China's latest patents, Technical Efficacy Thesaurus, Application Domain, Technology Topic, Popular Technical Reports.
© 2024 PatSnap. All rights reserved.Legal|Privacy policy|Modern Slavery Act Transparency Statement|Sitemap|About US| Contact US: help@patsnap.com