Belt-driven variable-drive kinematic chain and parallel robot with same
A variable drive and belt transmission technology, applied in manipulators, program-controlled manipulators, manufacturing tools, etc., can solve the problems of small working space, uncontrollable terminals, and increased mechanism volume, and achieve the effect of small system quality.
- Summary
- Abstract
- Description
- Claims
- Application Information
AI Technical Summary
Problems solved by technology
Method used
Image
Examples
Embodiment Construction
[0034]The implementation of the present invention will be described in detail below in conjunction with the drawings and examples.
[0035] A variable drive kinematic chain with belt transmission in the present invention is schematically shown as figure 1 As shown, the structural assembly diagram of the variable drive kinematic chain is shown in figure 2 shown. A variable drive kinematic chain with belt transmission includes a support module, a drive module, a drive switching device, a connecting rod assembly and a belt transmission system. The support module includes support plate 5, bearing seat I11 and bearing seat II12; the drive module includes servo motor 7, motor cover 8 and central shaft 23; the drive switching device includes electromagnetic brake I6, electromagnetic brake II9, electromagnetic clutch I10 and electromagnetic clutch II13; The connecting rod assembly includes a primary connecting rod 3 and a secondary connecting rod 4; the belt transmission system inc...
PUM
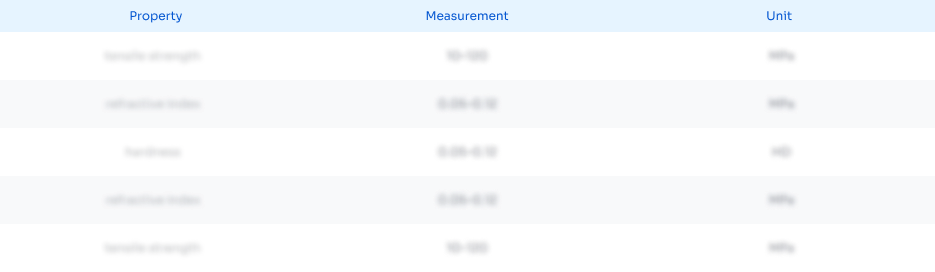
Abstract
Description
Claims
Application Information

- R&D
- Intellectual Property
- Life Sciences
- Materials
- Tech Scout
- Unparalleled Data Quality
- Higher Quality Content
- 60% Fewer Hallucinations
Browse by: Latest US Patents, China's latest patents, Technical Efficacy Thesaurus, Application Domain, Technology Topic, Popular Technical Reports.
© 2025 PatSnap. All rights reserved.Legal|Privacy policy|Modern Slavery Act Transparency Statement|Sitemap|About US| Contact US: help@patsnap.com