Dual-cavity self-thermal-insulation wall system obtained by splicing small jointed boards
A self-insulation and splicing technology, which is applied in the direction of thermal insulation, building thermal insulation materials, walls, etc., can solve the problems of inability to achieve self-insulation of walls and large floor space, save materials, reduce floor space, and achieve good thermal insulation performance. Effect
- Summary
- Abstract
- Description
- Claims
- Application Information
AI Technical Summary
Problems solved by technology
Method used
Image
Examples
Embodiment Construction
[0015] Such as Figure 1 to Figure 6 As shown, the double-cavity self-insulation wall system assembled by small pieces of panels includes upper beam 1, lower beam 5, connector 3, assembly board 2, cement glue 4 and waterproof layer 6, assembly board 2, connector 3 and The cement glue 4 is assembled together to form the main wall. The upper beam 1 and the lower beam 5 are respectively fixed on the upper and lower ends of the main wall. Leveling ruler, upper and lower beams, several reinforcing steel bars are installed between the upper and lower beams to make the wall more stable, leveling ruler, in the construction process to ensure the smooth splicing of the panels, and the cement glue is applied to the glue grooves and connectors of the panels It is used to fix the jigsaw panels, the connectors are plastic parts, used to insert the steel bars between the upper and lower parts and the three jigsaw panels, and two air layers are separated between the jigsaw panels to form a do...
PUM
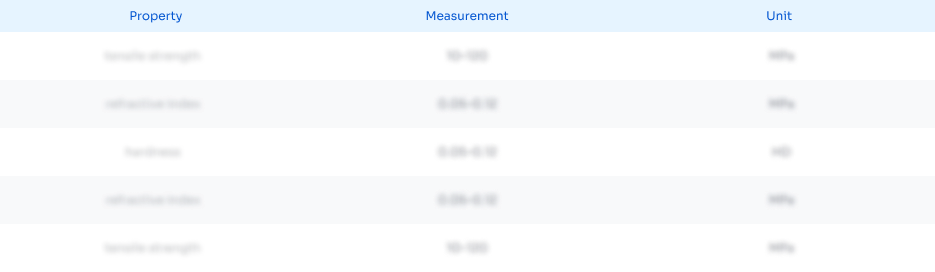
Abstract
Description
Claims
Application Information

- R&D
- Intellectual Property
- Life Sciences
- Materials
- Tech Scout
- Unparalleled Data Quality
- Higher Quality Content
- 60% Fewer Hallucinations
Browse by: Latest US Patents, China's latest patents, Technical Efficacy Thesaurus, Application Domain, Technology Topic, Popular Technical Reports.
© 2025 PatSnap. All rights reserved.Legal|Privacy policy|Modern Slavery Act Transparency Statement|Sitemap|About US| Contact US: help@patsnap.com