Method for reducing forging residual stress of turbine disks via gradient speed control on basis of numerical calculation
A residual stress, numerical calculation technology, applied in the direction of calculation, computer-aided design, special data processing applications, etc., can solve the problems of inability to meet the requirements of turbine disk forging process controllability, high cost, inaccurate test results, etc.
- Summary
- Abstract
- Description
- Claims
- Application Information
AI Technical Summary
Problems solved by technology
Method used
Image
Examples
Embodiment
[0032] In this example, for figure 1 The forming process of the turbine disk shown is studied, the diameter of the disk is 311mm, and the two-dimensional cross-sectional diagram is as follows figure 1 (a) shown. According to the forming dimensions of the turbine disk, considering the geometric characteristics and volume of the turbine disk, the geometric characteristics of the upper and lower dies in the forging process are designed, such as figure 1 (b) shown.
[0033] Considering the central symmetry of the forging die and the turbine disk, the numerical simulation of the forging process of the turbine disk is carried out in Deform2D, and only the axial section of the turbine disk and the forging die is selected for analysis. The initial blank of the turbine disc is a cylindrical blank, the near-isothermal forging temperature is 1010°C, the heating temperature of the mold equipment is 930°C, and a special lubricant is applied. In the creation of the geometric model, after...
PUM
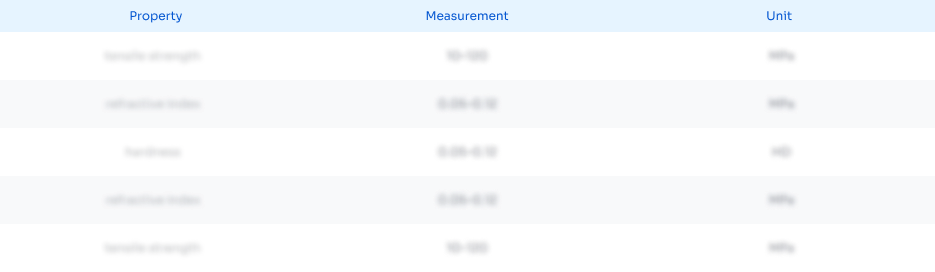
Abstract
Description
Claims
Application Information

- R&D
- Intellectual Property
- Life Sciences
- Materials
- Tech Scout
- Unparalleled Data Quality
- Higher Quality Content
- 60% Fewer Hallucinations
Browse by: Latest US Patents, China's latest patents, Technical Efficacy Thesaurus, Application Domain, Technology Topic, Popular Technical Reports.
© 2025 PatSnap. All rights reserved.Legal|Privacy policy|Modern Slavery Act Transparency Statement|Sitemap|About US| Contact US: help@patsnap.com