A kind of forging forming process of subway vehicle bearing seat
A forging molding and bearing seat technology, applied in the field of forging, can solve the problems of high product scrap rate, low service life of molds, and easy damage of molds, etc., so as to prolong the life of molds, increase pre-bending stations, and reduce the weight of blanking Effect
- Summary
- Abstract
- Description
- Claims
- Application Information
AI Technical Summary
Problems solved by technology
Method used
Image
Examples
Embodiment Construction
[0025] The embodiments of the present invention will be described in detail below with reference to the accompanying drawings, but the present invention can be implemented in many different ways defined and covered by the claims.
[0026] The shape of the product of the present invention is that the two ends are small and not on the same axis, and the middle is a U-shaped big foot shape. During the forging process, the metal flow is difficult and it is difficult to form. The invention provides a forging forming process of a subway bearing seat, see Figure 7 , including the following steps:
[0027] a. Cutting materials: select raw materials according to product requirements.
[0028] Because the bearing block manufactured by the process of the present invention is generally used on subway vehicles, it is an important supporting element on the bogie, and is used to support and fix the bearing. Because the size of such products is related to the vehicle model, the shape of th...
PUM
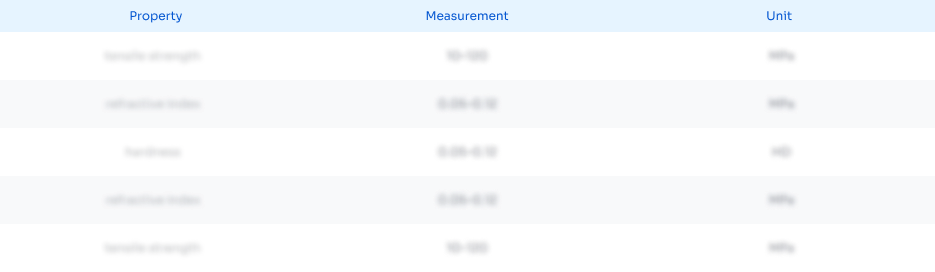
Abstract
Description
Claims
Application Information

- R&D
- Intellectual Property
- Life Sciences
- Materials
- Tech Scout
- Unparalleled Data Quality
- Higher Quality Content
- 60% Fewer Hallucinations
Browse by: Latest US Patents, China's latest patents, Technical Efficacy Thesaurus, Application Domain, Technology Topic, Popular Technical Reports.
© 2025 PatSnap. All rights reserved.Legal|Privacy policy|Modern Slavery Act Transparency Statement|Sitemap|About US| Contact US: help@patsnap.com