Damping brake device
A brake device and damping technology, which is applied in the direction of brake type, axial brake, brake parts, etc., can solve the problem of poor braking efficiency and heat dissipation of drum brakes, poor braking damping stability, small braking friction area, etc. problems, to achieve the effect of reducing impact, increasing brake damping force, and reducing impact noise
- Summary
- Abstract
- Description
- Claims
- Application Information
AI Technical Summary
Problems solved by technology
Method used
Image
Examples
Embodiment Construction
[0026] The present invention will be further described in detail below in conjunction with the accompanying drawings and embodiments.
[0027] This embodiment provides a damping braking device. In the damping braking device, the relative position of the rotating part and the damping part is fixed, and the installation is convenient; and when the rotating part rotates positively and negatively, it can play the role of braking and damping, and the braking in both directions The damping effect is the same.
[0028] like Figure 1-3 As shown, the damping braking device includes: a rotating member, a damping member, a friction member, a connecting member and a braking force applying member.
[0029] Among them, the rotating part includes: left mounting plate 19, stop disc 17 and connecting shaft 7; the damping part includes: damping disc 16 and compression cylinder 10; The right mounting plate 8 and the housing 21; the braking force applying member includes: the separator 1 and t...
PUM
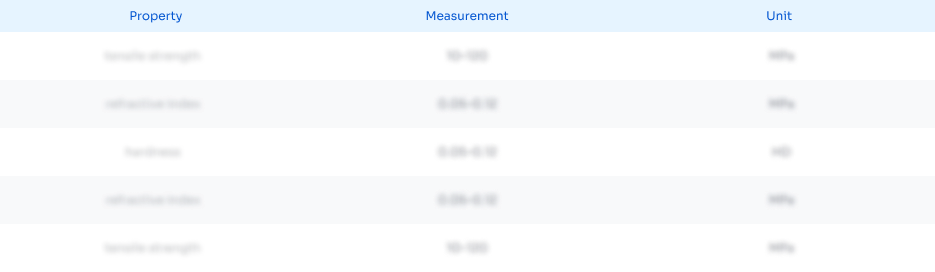
Abstract
Description
Claims
Application Information

- R&D Engineer
- R&D Manager
- IP Professional
- Industry Leading Data Capabilities
- Powerful AI technology
- Patent DNA Extraction
Browse by: Latest US Patents, China's latest patents, Technical Efficacy Thesaurus, Application Domain, Technology Topic, Popular Technical Reports.
© 2024 PatSnap. All rights reserved.Legal|Privacy policy|Modern Slavery Act Transparency Statement|Sitemap|About US| Contact US: help@patsnap.com