Knuckle bearing structure of mechanical elastic wheel
A technology of joint bearings and elastic wheels, which is applied in the direction of rotating bearings, bearings, wheels, etc., can solve the problems of large internal friction, loss, interference, etc. of the hinge, to improve high-speed service life, improve vibration and noise problems, and reduce friction The effect of energy loss
- Summary
- Abstract
- Description
- Claims
- Application Information
AI Technical Summary
Problems solved by technology
Method used
Image
Examples
Embodiment Construction
[0017] The present invention will be further described below in conjunction with the accompanying drawings.
[0018] Such as figure 1 As shown, the joint bearing structure of the mechanical elastic wheel of the present invention includes several interconnected high-speed joint bearings, and the high-speed joint bearing includes an outer ring housing 1 , balls 2 , inner ring 3 , and a sealing cover 4 . The inner side of the outer ring housing 1 is a concave spherical surface, and the outer side of the inner ring 3 is a convex spherical surface. Two annular raceways are arranged on the convex spherical surface of the inner ring 3, and the balls are closely arranged on the raceways. 2. The inner ring 3 is arranged in the outer ring housing 1, and the concave spherical surface of the outer ring housing 1 cooperates with two annular raceways on the outer convex spherical surface of the inner ring 3 to form the rolling path of the ball 2. road. The sealing cover 4 is installed on...
PUM
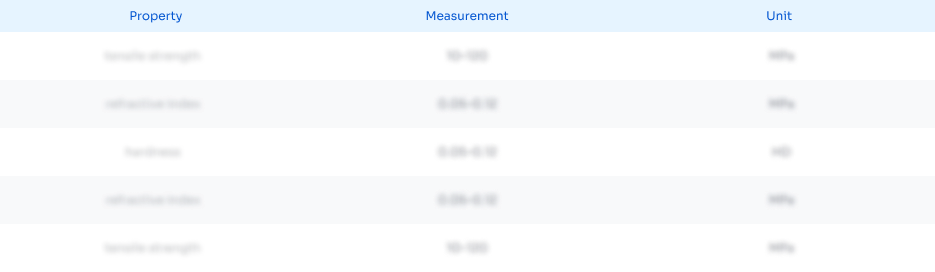
Abstract
Description
Claims
Application Information

- R&D
- Intellectual Property
- Life Sciences
- Materials
- Tech Scout
- Unparalleled Data Quality
- Higher Quality Content
- 60% Fewer Hallucinations
Browse by: Latest US Patents, China's latest patents, Technical Efficacy Thesaurus, Application Domain, Technology Topic, Popular Technical Reports.
© 2025 PatSnap. All rights reserved.Legal|Privacy policy|Modern Slavery Act Transparency Statement|Sitemap|About US| Contact US: help@patsnap.com