Preparing method of flame retardant plywood
A technology of plywood and flame retardant, which is used in the joining of wooden veneers, manufacturing tools, wood treatment, etc., can solve the problems of single, not achieving flame retardant effect, etc. tight and stable effect
- Summary
- Abstract
- Description
- Claims
- Application Information
AI Technical Summary
Problems solved by technology
Method used
Examples
Embodiment 1
[0020] A preparation method for flame retardant plywood, comprising the following steps:
[0021] 1) Log processing: sawing off the logs, cooking and peeling them, and cutting the peeled wood segments into chips.
[0022] 2) Primary drying: put the ring-cut wood chips into the drying room, and control the temperature at 55°C for 23 hours.
[0023] 3) Impregnation treatment: the flame retardant is made into an impregnation solution with a solution concentration of 5%, and the once-dried veneer is immersed in the impregnation solution for 6 hours.
[0024] 4) Gluing: Coating adhesive on each layer of wood chips;
[0025] 5) Pre-pressing: Assemble the wood chips, and then put them into a hot press for pre-pressing. The pre-pressing temperature is 52°C, the pressure is 4.5 MPa, and the pre-pressing time is 1.8 hours to obtain a raw board;
[0026] 6) Trimming and hot pressing: cut the rough board into a standard board, and then hot press, the hot pressing temperature is 103°C, t...
Embodiment 2
[0033] A preparation method for flame retardant plywood, comprising the following steps:
[0034] 1) Log processing: sawing off the logs, cooking and peeling them, and cutting the peeled wood segments into chips.
[0035] 2) Drying: put the ring-cut wood chips into the drying room, and control the temperature at 63°C for 15.5 hours.
[0036] 3) Impregnation treatment: the flame retardant is made into an impregnation solution with a solution concentration of 8%, and the once-dried veneer is immersed in the impregnation solution for 4 hours.
[0037] 4) Gluing: Coating adhesive on each layer of wood chips.
[0038] 5) Pre-pressing: Assemble the wood chips, and then put them into a hot press for pre-pressing. The pre-pressing temperature is 71° C., the pressure is 8.1 MPa, and the pre-pressing time is 0.8 hours to obtain a raw board.
[0039] 6) Trimming and hot-pressing: cut the rough board into a standard board, and then hot-press at a temperature of 107° C., a pressure of 15...
Embodiment 3
[0046] A preparation method for flame retardant plywood, comprising the following steps:
[0047] 1) Log processing: sawing off the logs, cooking and peeling them, and cutting the peeled wood segments into chips.
[0048] 2) Drying: Put the ring-cut wood chips into the drying room, and control the temperature at 80°C for 12 hours.
[0049] 3) Impregnation treatment: the flame retardant is made into an impregnation solution with a solution concentration of 10%, and the once-dried veneer is immersed in the impregnation solution for 3 hours.
[0050] 4) Gluing: Coating adhesive on each layer of wood chips.
[0051] 5) Pre-pressing: Assemble the wood chips, and then put them into a hot press for pre-pressing. The pre-pressing temperature is 75° C., the pressure is 10 MPa, and the pre-pressing time is 0.5 hours to obtain a raw board.
[0052] 6) Trimming and hot-pressing: cut the raw board into standard boards, and then hot-press. The hot-pressing temperature is 110° C., the pres...
PUM
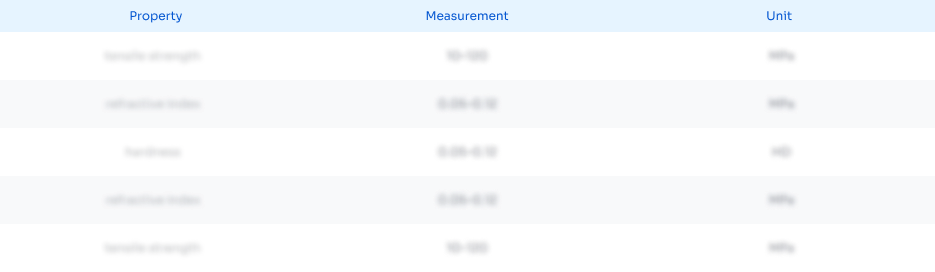
Abstract
Description
Claims
Application Information

- R&D Engineer
- R&D Manager
- IP Professional
- Industry Leading Data Capabilities
- Powerful AI technology
- Patent DNA Extraction
Browse by: Latest US Patents, China's latest patents, Technical Efficacy Thesaurus, Application Domain, Technology Topic, Popular Technical Reports.
© 2024 PatSnap. All rights reserved.Legal|Privacy policy|Modern Slavery Act Transparency Statement|Sitemap|About US| Contact US: help@patsnap.com