Self-forcing cooling high-temperature resisting mechanical sealing device
A mechanical seal device and high temperature resistant technology, which is applied in the direction of engine seal, mechanical equipment, engine components, etc., can solve the problems of mechanical seal friction pair end surface temperature rise, sealing surface leakage sealing, friction pair dry grinding, etc., to achieve enhanced heat dissipation ability, speed up medium flow rate, and prevent high temperature vaporization
- Summary
- Abstract
- Description
- Claims
- Application Information
AI Technical Summary
Problems solved by technology
Method used
Image
Examples
Embodiment Construction
[0038] Below in conjunction with accompanying drawing and specific embodiment content of the present invention is described in further detail:
[0039] The self-forced cooling and high-temperature resistant mechanical seal device provided by the present invention is mainly arranged between the pump inlet and the turbine of the turbo pump of the liquid rocket engine. The invention can also be used in sealing devices in the fields of ships and nuclear industries, and other rotating devices that must ensure sealing, have small size and space, require multiple starts and stops, and long life.
[0040] Such as Figure 1 to Figure 6 As shown, the self-forced cooling high temperature resistant mechanical seal device provided by the present invention mainly includes an O-shaped rubber ring 1, a moving ring 4, a graphite ring 5, a static ring seat 6, an annular diaphragm group 3, an annular housing 9, a heat insulation Ring 10.
[0041] The moving ring 4 is fixedly set on the end of ...
PUM
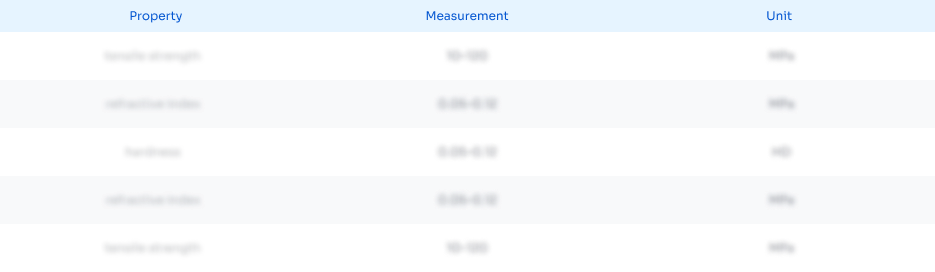
Abstract
Description
Claims
Application Information

- R&D
- Intellectual Property
- Life Sciences
- Materials
- Tech Scout
- Unparalleled Data Quality
- Higher Quality Content
- 60% Fewer Hallucinations
Browse by: Latest US Patents, China's latest patents, Technical Efficacy Thesaurus, Application Domain, Technology Topic, Popular Technical Reports.
© 2025 PatSnap. All rights reserved.Legal|Privacy policy|Modern Slavery Act Transparency Statement|Sitemap|About US| Contact US: help@patsnap.com