Non-toxic color superlight clay and manufacturing method thereof
A technology of ultra-light clay and color, which is applied in the field of production, processing and production of ultra-light clay. It can solve the problems that ultra-light clay cannot meet the quality requirements, the production environment is seriously polluted, and it cannot be stored for a long time. No pollution, easy styling effect
- Summary
- Abstract
- Description
- Claims
- Application Information
AI Technical Summary
Problems solved by technology
Method used
Examples
Embodiment 1
[0022] Formula: 8 parts of ultra-light physical microspheres, 18 parts of polyvinyl alcohol, 3 parts of water-soluble color paste, 0.5 parts of glycerin, 0.5 parts of antifreeze, 2 parts of Vaseline, and 60 parts of water.
[0023] The production method comprises the following specific steps:
[0024] (1) Put 18 parts of polyvinyl alcohol into the reaction kettle, heat and stir to 95°C, then stir at constant temperature for 4 hours to ensure that the polyvinyl alcohol particles are completely melted, then put the prepared polyvinyl alcohol solution into the container and let it cool spare;
[0025] (2) Take 9 parts of the cooled polyvinyl alcohol solution in step (1) and put it into the kneader, add 8 parts of ultra-light physical microspheres into the kneader for full stirring, so that the polyvinyl alcohol solution and the ultra-light physical Mix the microspheres thoroughly;
[0026] (3) Add the mixed solution of polyvinyl alcohol solution and ultra-light physical microsp...
Embodiment 2
[0029] Formula: 9 parts of ultra-light physical microspheres, 19 parts of polyvinyl alcohol, 4 parts of water-soluble color paste, 0.5 parts of propylene glycol, 0.5 parts of sorbitol, 1 part of antifreeze, 2.3 parts of Vaseline, and 65 parts of water.
[0030] The production method comprises the following specific steps:
[0031] (1) Put 19 parts of polyvinyl alcohol into the reaction kettle, heat and stir to 95°C, then stir at constant temperature for 4 hours to ensure that the polyvinyl alcohol particles are completely melted, then put the prepared polyvinyl alcohol solution into the container and let it cool spare;
[0032] (2) Take 9.5 parts of the cooled polyvinyl alcohol solution in step (1) and put it into the kneader, add 9 parts of ultra-light physical microspheres into the kneader for full stirring, so that the polyvinyl alcohol solution and the ultra-light physical Mix the microspheres thoroughly;
[0033] (3) Add the mixed solution of polyvinyl alcohol solution ...
Embodiment 3
[0036] Formula: 10 parts of ultra-light physical microspheres, 20 parts of polyvinyl alcohol, 5 parts of water-soluble color paste, 1.5 parts of propylene glycol, 1.5 parts of antifreeze, 2.5 parts of Vaseline, and 70 parts of water.
[0037] The production method comprises the following specific steps:
[0038] (1) Put 20 parts of polyvinyl alcohol into the reaction kettle, heat and stir to 95°C, then stir at constant temperature for 4 hours to ensure that the polyvinyl alcohol particles are completely melted, then put the prepared polyvinyl alcohol solution into the container and let it cool spare;
[0039] (2) Take 10 parts of the cooled polyvinyl alcohol solution in step (1) and put it into the kneader, add 10 parts of ultra-light physical microspheres into the kneader for full stirring, so that the polyvinyl alcohol solution and the ultra-light physical Mix the microspheres thoroughly;
[0040] (3) Add the mixed solution of polyvinyl alcohol solution and ultra-light phy...
PUM
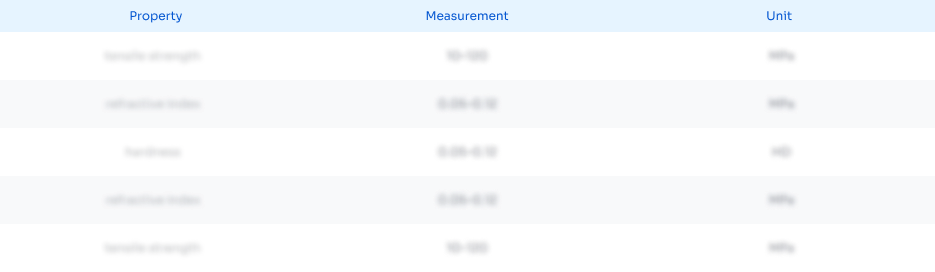
Abstract
Description
Claims
Application Information

- R&D
- Intellectual Property
- Life Sciences
- Materials
- Tech Scout
- Unparalleled Data Quality
- Higher Quality Content
- 60% Fewer Hallucinations
Browse by: Latest US Patents, China's latest patents, Technical Efficacy Thesaurus, Application Domain, Technology Topic, Popular Technical Reports.
© 2025 PatSnap. All rights reserved.Legal|Privacy policy|Modern Slavery Act Transparency Statement|Sitemap|About US| Contact US: help@patsnap.com