Method for improving identification precision of kinetic parameters of modularized robot joint
A technology of robot joints and dynamic parameters, applied in instruments, control/adjustment systems, adaptive control, etc., can solve the problems of inaccurate parameter identification and measurement, measurement accuracy dependent on motor performance, inaccuracy, etc., and achieve a small amount of calculation Effect
- Summary
- Abstract
- Description
- Claims
- Application Information
AI Technical Summary
Problems solved by technology
Method used
Image
Examples
Embodiment 1
[0053] A method for improving the identification accuracy of modular robot joint dynamic parameters by a modular robot joint dynamic parameter identification accuracy improvement device, such as figure 2 , including the following steps,
[0054] S1. The Newton-Euler method is used for dynamic modeling. Step S1 specifically includes:
[0055] S11. Set the coordinate system, and establish the joint dynamics model according to the Newton-Euler formula:
[0056]
[0057] In the formula, F represents the force on the center of mass, m represents the mass of the rigid body, represents the acceleration, I represents the inertia tensor of the rigid body in the coordinate system, ω represents the angular velocity of the rigid body’s rotation, Indicates the angular acceleration of the rigid body rotation.
[0058] S12. Simplify the derivation of the above formula to obtain the general equivalent form of the joint dynamics equation:
[0059]
[0060] S13. Rewrite the linear...
Embodiment 2
[0077] A method for improving the identification accuracy of a modular robot joint dynamic parameter identification accuracy of a modular robot joint dynamic parameter identification accuracy improvement device, specifically comprising the following steps,
[0078] S1. Establish the stiffness identification equation according to the principle of torsion spring:
[0079] τ=K·Δq=K(q-q 0 )
[0080] Among them, Δq represents the amount of torsion angle deformation, q represents the joint angle value, and q 0 Indicates the motor end angle value.
[0081] S2. Apply the improved Fourier series excitation trajectory to the device for improving the identification accuracy of the joint dynamic parameters of the modular robot; the excitation trajectory function in step S2 is:
[0082]
[0083] Among them, t f = 2π / ω f , j=INT(t / t f ), q(0)=q init ,q(t f )=q init ,
[0084] In the formula, i represents the number of i-th joints, t represents time, m is an integer, ω f Repr...
PUM
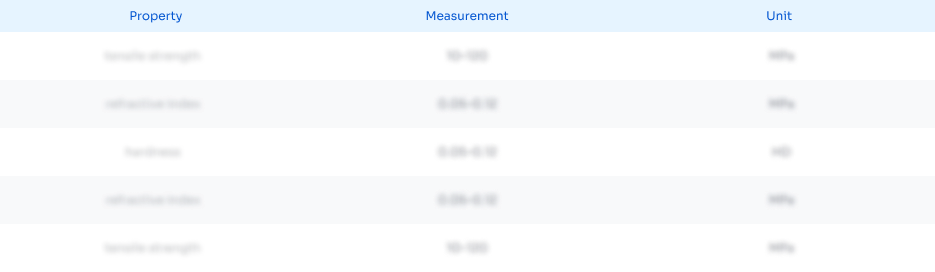
Abstract
Description
Claims
Application Information

- R&D
- Intellectual Property
- Life Sciences
- Materials
- Tech Scout
- Unparalleled Data Quality
- Higher Quality Content
- 60% Fewer Hallucinations
Browse by: Latest US Patents, China's latest patents, Technical Efficacy Thesaurus, Application Domain, Technology Topic, Popular Technical Reports.
© 2025 PatSnap. All rights reserved.Legal|Privacy policy|Modern Slavery Act Transparency Statement|Sitemap|About US| Contact US: help@patsnap.com