3D (three-dimensional) printing stack forming ballast bed elevation adjusting method
A 3D printing and surface adjustment technology, which is applied to roads, tracks, ballast layers, etc., can solve the problems of waste of filling materials, weak track structure, and multiple construction efficiency, and achieves small on-site workload, reduction of bases, and digital intelligence. high degree of effect
- Summary
- Abstract
- Description
- Claims
- Application Information
AI Technical Summary
Problems solved by technology
Method used
Image
Examples
Embodiment Construction
[0044] The present invention will be described in detail below in conjunction with specific embodiments.
[0045] Such as figure 1 As shown, the method for adjusting the elevation of the ballast bed surface by 3D printing stacking forming of the present invention comprises the following steps:
[0046] (1) Establish a three-dimensional map of the elevation of the base surface; measure the elevation of the base surface in sections based on the slope adjustment diagram designed based on the line penetration survey and the tunnel section results, the poured base of the track construction drawing, and the layout of the prefabricated components. Establish a three-dimensional map mathematical model of the elevation of the base surface;
[0047] (2) Establish a three-dimensional digital model of prefabricated components; measure the flatness of the lower surface of each prefabricated component, and establish a three-dimensional mathematical model of the flatness of the lower surface...
PUM
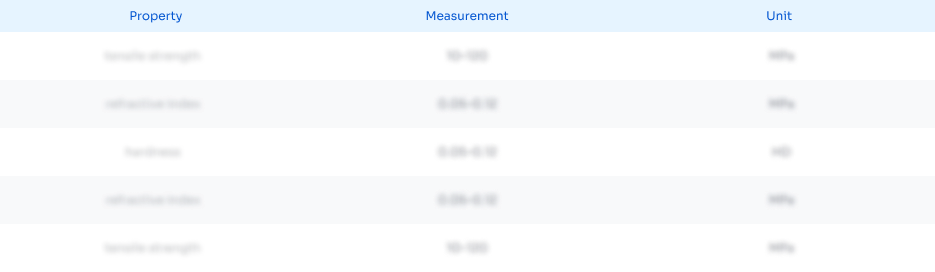
Abstract
Description
Claims
Application Information

- Generate Ideas
- Intellectual Property
- Life Sciences
- Materials
- Tech Scout
- Unparalleled Data Quality
- Higher Quality Content
- 60% Fewer Hallucinations
Browse by: Latest US Patents, China's latest patents, Technical Efficacy Thesaurus, Application Domain, Technology Topic, Popular Technical Reports.
© 2025 PatSnap. All rights reserved.Legal|Privacy policy|Modern Slavery Act Transparency Statement|Sitemap|About US| Contact US: help@patsnap.com