Inlet tension feed forward compensation method and system adopting monitoring automatic gauge control (AGC)
A technology of thickness control and feedforward compensation, applied in rolling mill control device, tension/pressure control, metal rolling, etc., can solve the problems of decreased product yield, increase of strip out-of-tolerance length, influence of control accuracy, etc. Accuracy, improve yield, weaken the effect of strong coupling relationship
- Summary
- Abstract
- Description
- Claims
- Application Information
AI Technical Summary
Problems solved by technology
Method used
Image
Examples
Embodiment Construction
[0039] The present invention will be further described below in conjunction with specific examples and accompanying drawings.
[0040] like figure 1As shown, the strip steel 7 is uncoiled from the entrance coiler 1, enters the six-roll mill 8 after passing through the entrance turning roll 2 for rolling, passes through the exit turning roll 13 after rolling, and is coiled on the exit coiler 15, and the strip steel 7 Thickness control is programmed in the process PLC controller 14, and the process PLC controller 14 controls the hydraulic cylinder 5 to provide rolling force to roll the strip steel 7 to the required thickness; the entrance and exit are configured to measure the thickness of the strip steel 7 at the entrance and exit The entrance thickness gauge 4 and the exit thickness gauge 11, the entrance and exit are also equipped with an entrance tension gauge 3 and an exit tension gauge 12 for measuring the tension at the entrance and exit of the strip steel 7; the entrance...
PUM
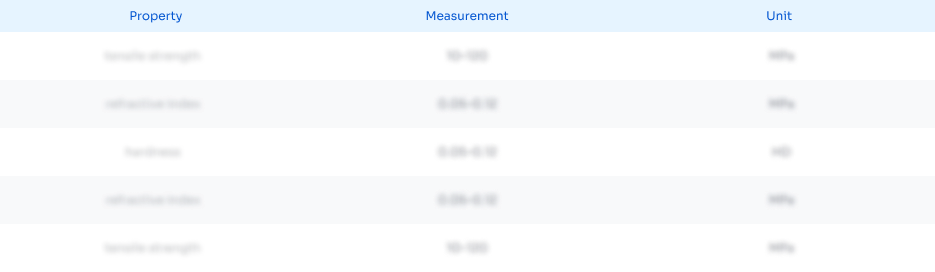
Abstract
Description
Claims
Application Information

- R&D
- Intellectual Property
- Life Sciences
- Materials
- Tech Scout
- Unparalleled Data Quality
- Higher Quality Content
- 60% Fewer Hallucinations
Browse by: Latest US Patents, China's latest patents, Technical Efficacy Thesaurus, Application Domain, Technology Topic, Popular Technical Reports.
© 2025 PatSnap. All rights reserved.Legal|Privacy policy|Modern Slavery Act Transparency Statement|Sitemap|About US| Contact US: help@patsnap.com