Core glaze for matte sand streak enamel glaze and production method thereof
An enamel glaze and sand pattern technology, which is applied in the field of matt sand pattern enamel glaze core glaze and production methods, can solve the problems of mass production restrictions and other issues
- Summary
- Abstract
- Description
- Claims
- Application Information
AI Technical Summary
Problems solved by technology
Method used
Examples
Embodiment 1
[0012] A matte sand pattern enamel core glaze material of the present invention contains the following components by weight percentage: 22% of quartz sand; 30% of magnesium oxide; 20% of soda ash; 15.98% of potassium feldspar; 2% of borax; 2%; calcium carbonate 3%; trisodium phosphate 5%; cobalt oxide 0.02%;
[0013] A method for producing the core glaze material of matt sand pattern enamel glaze, which comprises pulverizing quartz sand, magnesium oxide, soda ash, potassium feldspar, borax, fluorite, calcium carbonate, trisodium phosphate and cobalt oxide into Particles below 5 mm, mixed evenly, put into a high-temperature furnace at 1300 degrees Celsius to melt and keep for more than 30 minutes, take out the melted glaze and quench it with water to form coarse particles and then pack it into bags; when enameling metal plates, take matt sand Pattern enamel glaze core glaze 20-25%, bright glaze about 60-65%, aluminum hydroxide about 1.5-2.5%, clay about 4-6%, and the rest is co...
Embodiment 2
[0015] A matt sand pattern enamel core glaze, which contains the following components by weight percentage: 33% of quartz sand; 22% of magnesium oxide; 24.9% of soda ash; 8% of potassium feldspar; 5% of borax; 2% of fluorite ; Calcium carbonate 3%; Trisodium phosphate 2%; Cobalt oxide 0.1%;
[0016] A method for producing the core glaze material of matt sand pattern enamel glaze, which comprises pulverizing quartz sand, magnesium oxide, soda ash, potassium feldspar, borax, fluorite, calcium carbonate, trisodium phosphate and cobalt oxide into Particles below 5 mm, mixed evenly, put into a high-temperature furnace at 1300 degrees Celsius to melt and keep for more than 30 minutes, take out the melted glaze and quench it with water to form coarse particles and then pack it into bags; when enameling metal plates, take matt sand Pattern enamel glaze core glaze 20-25%, bright glaze about 60-65%, aluminum hydroxide about 1.5-2.5%, clay about 4-6%, and the rest is colorant and water, ...
Embodiment 3
[0018] A matt sand texture enamel core glaze, which contains the following components by weight percentage: 28% of quartz sand; 26% of magnesium oxide; 24% of soda ash; 12% of potassium feldspar; 3% of borax; 1.44% of fluorite ; Calcium carbonate 2%; Trisodium phosphate 3.5%; Cobalt oxide 0.06%;
[0019] A method for producing the core glaze material of matt sand pattern enamel glaze, which comprises pulverizing quartz sand, magnesium oxide, soda ash, potassium feldspar, borax, fluorite, calcium carbonate, trisodium phosphate and cobalt oxide into Particles below 5 mm, mixed evenly, put into a high-temperature furnace at 1300 degrees Celsius to melt and keep for more than 30 minutes, take out the melted glaze and quench it with water to form coarse particles and then pack it into bags; when enameling metal plates, take matt sand Pattern enamel glaze core glaze 20-25%, bright glaze about 60-65%, aluminum hydroxide about 1.5-2.5%, clay about 4-6%, and the rest is colorant and wa...
PUM
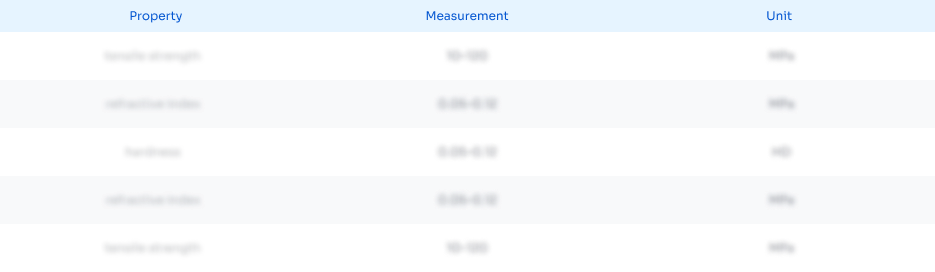
Abstract
Description
Claims
Application Information

- R&D
- Intellectual Property
- Life Sciences
- Materials
- Tech Scout
- Unparalleled Data Quality
- Higher Quality Content
- 60% Fewer Hallucinations
Browse by: Latest US Patents, China's latest patents, Technical Efficacy Thesaurus, Application Domain, Technology Topic, Popular Technical Reports.
© 2025 PatSnap. All rights reserved.Legal|Privacy policy|Modern Slavery Act Transparency Statement|Sitemap|About US| Contact US: help@patsnap.com