Auxiliary spinning forming tool for thin-wall aluminum alloy end socket baffle and forming process of auxiliary spinning forming tool
A spinning forming, aluminum alloy technology, applied in the field of auto parts processing, can solve the problems of large wall thickness reduction rate of components, flange instability and wrinkling, reducing production efficiency, etc., to achieve easy implementation and solve wrinkling defects , the effect of improving production efficiency
- Summary
- Abstract
- Description
- Claims
- Application Information
AI Technical Summary
Problems solved by technology
Method used
Image
Examples
Embodiment Construction
[0026] The present invention will be further described in detail below with reference to the embodiments of the accompanying drawings.
[0027] As shown in the drawings, this embodiment is a thin-walled aluminum alloy head baffle auxiliary spinning forming tool, including a core mold 1, the core mold is a hollow cover, set on the main shaft of the machine tool, and the main shaft of the machine tool can be Driven by the motor, it rotates rapidly, thereby driving the mandrel set on the main shaft to rotate rapidly. An arc surface is formed on the mandrel, and the contour of the arc surface is consistent with the contour of the inner wall of the final product. When spinning the flange blank, the flange blank gradually follows the circular arc under the local continuous pressure of the spinning wheel. In the arc surface film forming, the mandrel mainly plays the role of guiding and supporting the blank in the spinning process.
[0028] A columnar tail top 2 is arranged on the to...
PUM
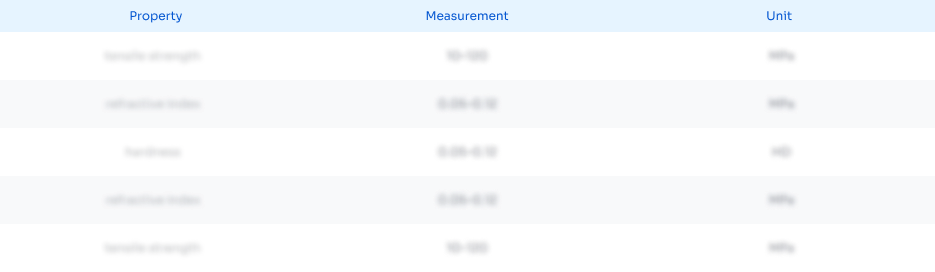
Abstract
Description
Claims
Application Information

- R&D
- Intellectual Property
- Life Sciences
- Materials
- Tech Scout
- Unparalleled Data Quality
- Higher Quality Content
- 60% Fewer Hallucinations
Browse by: Latest US Patents, China's latest patents, Technical Efficacy Thesaurus, Application Domain, Technology Topic, Popular Technical Reports.
© 2025 PatSnap. All rights reserved.Legal|Privacy policy|Modern Slavery Act Transparency Statement|Sitemap|About US| Contact US: help@patsnap.com