High-accuracy composite material structure damage monitoring method
A technology for composite materials and structural damage, which is applied in the analysis of materials, material analysis using sonic/ultrasonic/infrasonic waves, and measurement devices. It can solve problems affecting the accuracy of monitoring results, lack of mixed-signal separation methods, etc. Economic benefits, improved damage monitoring efficiency, and the effect of reducing polling times
- Summary
- Abstract
- Description
- Claims
- Application Information
AI Technical Summary
Problems solved by technology
Method used
Image
Examples
Embodiment Construction
[0026] The technical solutions of the present invention will be further described in detail below in conjunction with specific embodiments.
[0027] see figure 1 , a method for monitoring damage of a composite material structure with high accuracy, comprising the following steps: Step 101: uniformly arrange a plurality of piezoelectric sensors in the composite material structure to be tested to form a network of piezoelectric sensors.
[0028] The number and arrangement of piezoelectric sensors that make up the piezoelectric sensor network are determined according to actual needs. In the process of arranging piezoelectric sensors, it is necessary to ensure that the arrangement is as uniform as possible;
[0029] Step 102: selecting a plurality of pressure sensors for impact monitoring of the composite material structure under test in the sensor network as impact monitoring pressure sensors.
[0030] In this step, the entire piezoelectric sensor network arranged in the composi...
PUM
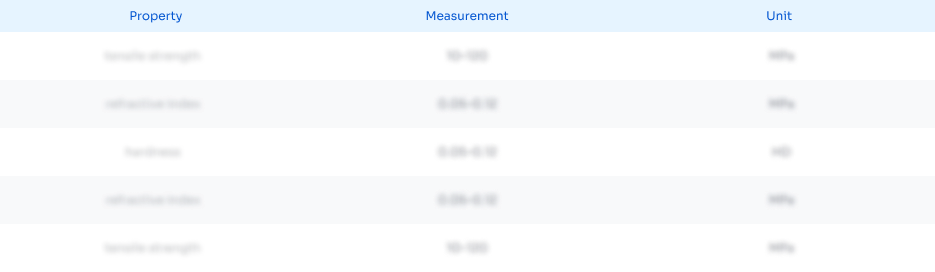
Abstract
Description
Claims
Application Information

- R&D Engineer
- R&D Manager
- IP Professional
- Industry Leading Data Capabilities
- Powerful AI technology
- Patent DNA Extraction
Browse by: Latest US Patents, China's latest patents, Technical Efficacy Thesaurus, Application Domain, Technology Topic, Popular Technical Reports.
© 2024 PatSnap. All rights reserved.Legal|Privacy policy|Modern Slavery Act Transparency Statement|Sitemap|About US| Contact US: help@patsnap.com