Thermal environment control structure and method for fused deposition process of 3D printer
A 3D printer, fused deposition technology, applied in 3D object support structure, processing environment adjustment, additive manufacturing, etc., can solve the problems of reduced service life and reliability, bulky insulation cabin structure, high temperature aging, etc., to control the bond strength. and deformation degree, good thermal environment control effect, and low comprehensive energy consumption
- Summary
- Abstract
- Description
- Claims
- Application Information
AI Technical Summary
Problems solved by technology
Method used
Image
Examples
Embodiment Construction
[0019] The present invention will be further described below in conjunction with accompanying drawing:
[0020] figure 1 Among them, there is a base 2 in the melting extrusion head 1, the base 2 is connected with the servo wire feeding mechanism 3, the servo wire feeding mechanism 3 is connected with the heat dissipation guide tube 4, the heat dissipation guide tube 4 is connected with the high temperature extrusion head 5, and the high temperature extrusion There is a constant temperature heating block 6 on the head 5, and the ring-shaped light-emitting board 7 is connected to the base 2 through a bracket 8. The center of the ring-shaped light-emitting board 7 is aligned with the axis of the high-temperature extrusion head 5. The center passes through the annular luminous plate 7, and there is a slight height difference between the tip of the high-temperature extrusion head 5 and the lower surface of the annular luminous plate 7, so that when the tip of the high-temperature e...
PUM
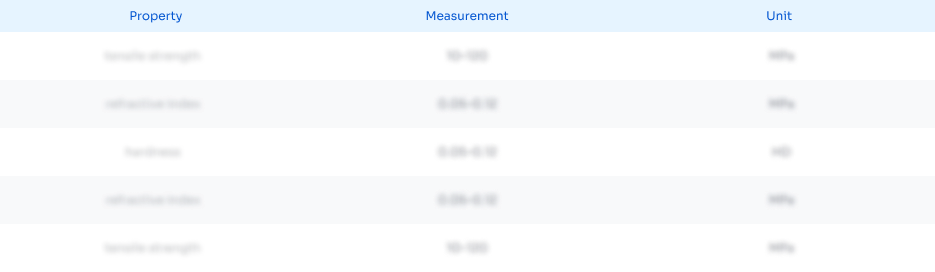
Abstract
Description
Claims
Application Information

- R&D Engineer
- R&D Manager
- IP Professional
- Industry Leading Data Capabilities
- Powerful AI technology
- Patent DNA Extraction
Browse by: Latest US Patents, China's latest patents, Technical Efficacy Thesaurus, Application Domain, Technology Topic, Popular Technical Reports.
© 2024 PatSnap. All rights reserved.Legal|Privacy policy|Modern Slavery Act Transparency Statement|Sitemap|About US| Contact US: help@patsnap.com