Modified ABS material for 3D printing machine and preparation method thereof
An ABS material, 3D printer technology, applied in additive processing and other directions, can solve the problems of weak mechanical properties of molding materials, low thermal deformation temperature, low ABS toughness, etc., to improve thermal stability, good mechanical properties, and reduce friction. The effect of resistance
- Summary
- Abstract
- Description
- Claims
- Application Information
AI Technical Summary
Problems solved by technology
Method used
Image
Examples
Example Embodiment
[0025] Example one:
[0026] The modified ABS material for 3D printers is composed of the following components in mass percentage: ABS 60%, ASA 39%, antioxidant 0.1%, lubricant 0.1%, and surfactant 0.8%.
[0027] The preparation method is as follows: a. Weigh parts by weight of ABS, ASA, antioxidants, lubricants and surfactant raw materials, dry them, and reserve them for use; b. Place each component raw material in step a in a high-speed disperser for high-speed dispersion C. Extruding the raw materials dispersed in step b in a twin-screw extruder to obtain modified ABS strips; d. cooling and air-drying the strips in step c, and rewinding the strips after air drying After rewinding, it is placed in a vacuum oven and dried again to obtain a modified ABS material for 3D printers.
[0028] In step b, the rotation speed of the high-speed disperser is 2000r / min, and the high-speed dispersion time is 25min; in step c, the temperature of the feed section, extrusion section and die head of...
Example Embodiment
[0029] Embodiment two:
[0030] The modified ABS material for 3D printers is composed of the following components in mass percentage: ABS 70%, ASA 29%, antioxidant 0.1%, lubricant 0.1%, and surfactant 0.8%.
[0031] The preparation method is as follows: a. Weigh ABS, ASA, antioxidants, lubricants and surfactant raw materials in parts by weight, dry them and reserve them for use; b. Place each component raw material in step a in a high-speed disperser for high-speed dispersion C. Extruding the raw materials dispersed in step b in a twin-screw extruder to obtain modified ABS strips; d. cooling and air-drying the strips in step c, and winding the strips after air drying After rewinding, it is placed in a vacuum oven and dried again to obtain modified ABS material for 3D printer.
[0032] In step b, the speed of the high-speed disperser is 2000r / min, and the high-speed dispersion time is 25min; in step c, the temperature of the feed section, extrusion section and die head of the twin-sc...
Example Embodiment
[0033] Example three:
[0034] The modified ABS material for 3D printers is composed of the following components in mass percentage: ABS 50%, ASA49%, antioxidant 0.1%, lubricant 0.1%, and surfactant 0.8%.
[0035] The preparation method is as follows: a. Weigh ABS, ASA, antioxidants, lubricants and surfactant raw materials in parts by weight, dry them and reserve them for use; b. Place each component raw material in step a in a high-speed disperser for high-speed dispersion C. Extruding the raw materials dispersed in step b in a twin-screw extruder to obtain modified ABS strips; d. cooling and air-drying the strips in step c, and winding the strips after air drying After rewinding, it is placed in a vacuum oven and dried again to obtain a modified ABS material for 3D printers.
[0036] In step b, the speed of the high-speed disperser is 2000r / min, and the high-speed dispersion time is 25min; in step c, the temperature of the feed section, extrusion section and die head of the twin-s...
PUM
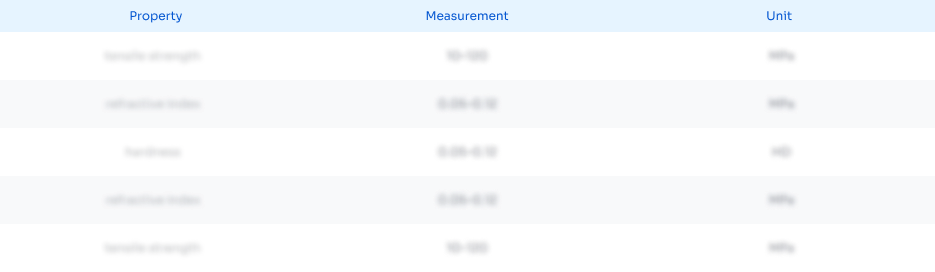
Abstract
Description
Claims
Application Information

- R&D Engineer
- R&D Manager
- IP Professional
- Industry Leading Data Capabilities
- Powerful AI technology
- Patent DNA Extraction
Browse by: Latest US Patents, China's latest patents, Technical Efficacy Thesaurus, Application Domain, Technology Topic.
© 2024 PatSnap. All rights reserved.Legal|Privacy policy|Modern Slavery Act Transparency Statement|Sitemap