A kind of synthetic method of styrene-modified dicyclopentadiene hydrogenation resin
A technology of dicyclopentadiene and hydrogenated resin, which is applied in the field of preparation of styrene-modified resin, can solve problems such as difficult to characterize, difficult to determine the composition of batch feeding, and difficult to produce consistent hot resin products, etc., reaching the price Moderate, low double bond content, reduce equipment investment costs and operating costs
- Summary
- Abstract
- Description
- Claims
- Application Information
AI Technical Summary
Problems solved by technology
Method used
Examples
Embodiment 1
[0030] Polymerization: Dry the 10L reactor, take analytically pure styrene: dicyclopentadiene (produced by Shandong Yuhuang Chemical Co., Ltd., batch number 20150305, mass fraction 85%): cyclohexane = 1:10:10, add after drying The 10L reactor was replaced with nitrogen for several times to remove the oxygen in the reactor, and the stirring paddle was started to heat the raw materials, thermally polymerized at 240°C for 2-6h, cooled down to room temperature, and the dicyclopentadiene resin liquid was obtained for use.
[0031] Hydrogenation: add an appropriate amount of catalyst to the reaction kettle, replace the oxygen in the reaction kettle with hydrogen several times, start the stirring paddle to heat the raw material, raise the temperature to 160°C, feed hydrogen, increase the pressure to 5MPa, and the hydrogenation temperature is 200°C, the reaction React for 2-6h under the condition of pressure of 5MPa. The above-mentioned catalyst is a nickel-supported catalyst, and the...
Embodiment 2
[0034] Polymerization: Dry the 10L reactor, take analytically pure styrene: dicyclopentadiene (produced by Shandong Yuhuang Chemical Co., Ltd., batch number 20150305, mass fraction 85%): cyclohexane = 1:10:10, add after drying The 10L reactor was replaced with nitrogen several times to remove the oxygen in the reactor, and the stirring paddle was started to heat the raw materials, thermally polymerized at 260°C for 2-6h, cooled down to room temperature, and dicyclopentadiene resin liquid was obtained for later use.
[0035] Hydrogenation: add an appropriate amount of catalyst to the reaction kettle, replace the oxygen in the reaction kettle with hydrogen several times, start the stirring paddle to heat the raw material, raise the temperature to 160°C, feed hydrogen, increase the pressure to 5MPa, and the hydrogenation temperature is 200°C, the reaction React for 2-6h under the condition of pressure of 5MPa. The above-mentioned catalyst is a nickel-supported catalyst, and the m...
Embodiment 3
[0038] Polymerization: Dry the 10L reactor, take analytically pure styrene: dicyclopentadiene (produced by Shandong Yuhuang Chemical Co., Ltd., batch number 20150305, mass fraction 85%): cyclohexane = 1:10:10, add after drying The 10L reactor was replaced with nitrogen several times to remove the oxygen in the reactor, and the stirring paddle was started to heat the raw materials, and the thermal polymerization reaction was carried out at 280°C for 2-6h, and cooled down to room temperature to obtain a dicyclopentadiene resin liquid for later use.
[0039] Hydrogenation: add an appropriate amount of catalyst to the reaction kettle, replace the oxygen in the reaction kettle with hydrogen several times, start the stirring paddle to heat the raw material, raise the temperature to 160°C, feed hydrogen, increase the pressure to 5MPa, and the hydrogenation temperature is 200°C, the reaction React for 2-6h under the condition of pressure of 5MPa. The above-mentioned catalyst is a nick...
PUM
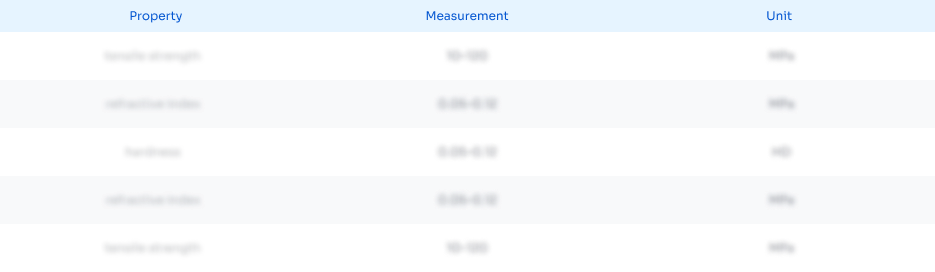
Abstract
Description
Claims
Application Information

- Generate Ideas
- Intellectual Property
- Life Sciences
- Materials
- Tech Scout
- Unparalleled Data Quality
- Higher Quality Content
- 60% Fewer Hallucinations
Browse by: Latest US Patents, China's latest patents, Technical Efficacy Thesaurus, Application Domain, Technology Topic, Popular Technical Reports.
© 2025 PatSnap. All rights reserved.Legal|Privacy policy|Modern Slavery Act Transparency Statement|Sitemap|About US| Contact US: help@patsnap.com