Method for preparing metal lamination material
A technology of metal and metal parts, applied in the field of titanium-containing metal laminated materials and preparation, can solve problems such as damage, lack of versatility, waste, etc., and achieve the effect of simple process and flexible process
- Summary
- Abstract
- Description
- Claims
- Application Information
AI Technical Summary
Benefits of technology
Problems solved by technology
Method used
Image
Examples
Embodiment approach
[0159] Vacuum or inert atmosphere are only preferred embodiments to prevent oxidation of metals, the inventors have found that sealing welding and / or pressing can be carried out entirely in atmospheric atmosphere. On the one hand, the inventors found that due to the close contact or close distance between the metal parts, the influence of oxygen is limited, and even without sealing and welding, it is still very difficult to exchange with the outside air. On the other hand, after the metal parts are sealed and welded together, the contact surface is airtightly isolated from the outside world, and there is little oxygen in the sealed space, which has little effect. According to one embodiment of the invention, the method of the invention does not comprise a vacuum step. According to one embodiment of the invention, the method of the invention does not comprise the step of replacing the air with an inert gas.
[0160] Seal welding of the edge 18 can be done in a manner known in ...
Embodiment 1
[0193] Two metal plates, industrially pure titanium TA1 and titanium alloy TC4 (Ti-6Al-4V), are used to clean the surface to remove all surface oxide layers and impurities. Such as figure 1 As shown, the two metal plates are stacked alternately. Pre-pressing is carried out on a hydraulic press so that the metal sheets are in close contact.
[0194] Using argon arc welding, the edges 18 of the contact surface between the two metal plates are hermetically welded together so that the contact surface or space between the two metal plates is airtightly isolated from the outside world to form a laminated body 10 .
[0195] The laminated body 10 was placed in a heating furnace and heated to 1650°C.
[0196] Such as Figure 2A As shown, the heated laminate 10 is high pressure pressed on a 100 ton hydraulic press with a pressure of 4 tons. After pressing, the two metal plates are forged and welded together to form a single billet.
Embodiment 2 to Embodiment 5
[0198] The same steps as in Example 1 were used, except that the metal materials listed in Table 1 were used.
PUM
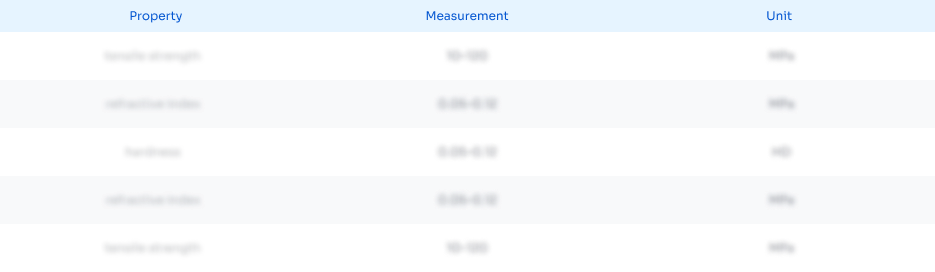
Abstract
Description
Claims
Application Information

- R&D Engineer
- R&D Manager
- IP Professional
- Industry Leading Data Capabilities
- Powerful AI technology
- Patent DNA Extraction
Browse by: Latest US Patents, China's latest patents, Technical Efficacy Thesaurus, Application Domain, Technology Topic, Popular Technical Reports.
© 2024 PatSnap. All rights reserved.Legal|Privacy policy|Modern Slavery Act Transparency Statement|Sitemap|About US| Contact US: help@patsnap.com