Membrane tension control device for stacking machine
A tension control and lamination machine technology, applied in the field of manufacturing equipment, can solve the problems of affecting quality, diaphragm wrinkling, tearing diaphragm, etc., to achieve high precision, constant tension and good stability.
- Summary
- Abstract
- Description
- Claims
- Application Information
AI Technical Summary
Problems solved by technology
Method used
Image
Examples
Embodiment Construction
[0035] The present invention will be further described below in conjunction with specific embodiments and accompanying drawings.
[0036] See Figure 1-3 As shown, it is a diaphragm tension control device for a laminated machine, which includes: a base 11, a riser assembly 5 mounted on the base 11, a servo motor 1 arranged on the riser assembly 5, a 5 and connected to the servo motor 1, the roller set 7 installed on the vertical plate assembly 5 and used to guide the diaphragm 10, the diaphragm tension control device of the stacker also includes a diaphragm tension control mechanism 16. The diaphragm tension control mechanism 16 includes the guide slide rail 12 installed on the front end of the vertical plate assembly 5, the moving seat 904 installed on the guide slide rail 12 and the floating roller group 9 installed on the moving seat 904, and the vertical plate assembly 5 rear end and is used to drive the cylinder 3 of the moving seat 904 and the floating roller group 9 to...
PUM
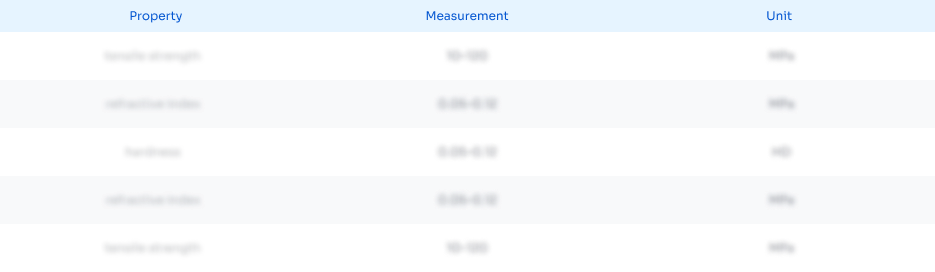
Abstract
Description
Claims
Application Information

- R&D
- Intellectual Property
- Life Sciences
- Materials
- Tech Scout
- Unparalleled Data Quality
- Higher Quality Content
- 60% Fewer Hallucinations
Browse by: Latest US Patents, China's latest patents, Technical Efficacy Thesaurus, Application Domain, Technology Topic, Popular Technical Reports.
© 2025 PatSnap. All rights reserved.Legal|Privacy policy|Modern Slavery Act Transparency Statement|Sitemap|About US| Contact US: help@patsnap.com