Preparation method of high-strength mullite castable
A technology of mullite and castables, which is applied in the field of refractory material processing, can solve the problems of production process influence, strength and stability not conforming to actual production, etc., and achieve the effects of ensuring properties, improving product quality, and improving strength
- Summary
- Abstract
- Description
- Claims
- Application Information
AI Technical Summary
Problems solved by technology
Method used
Examples
Embodiment 1
[0018] A method for preparing a high-strength mullite castable, comprising the following steps:
[0019] a. Put mullite, brown corundum, and zirconium materials into a crusher for crushing. After being crushed into granules, put the granules into a mixer and add water for stirring. The stirring time is 10 minutes to obtain mixed granules A;
[0020] b Put the SiO2 micropowder, heat-resistant steel fiber, and nano-barite powder into a ball mill and mix them for 20 minutes to make them mix evenly and fully to obtain the mixture B;
[0021] c. Put the mixed particle A and the mixed material B into a vacuum mixer, add the binder and water, and stir for 50 minutes under vacuum conditions to obtain the mixed material C;
[0022] d Pour the mixture C into a clean fixed mould, use a vibrating rod to vibrate and shape in layers, and wait until the surface is flooded, and the product is ready;
[0023] The above raw materials are calculated by weight: 40 parts of mullite, 30 parts of b...
Embodiment 2
[0028] A method for preparing a high-strength mullite castable, comprising the following steps:
[0029] a. Put mullite, brown corundum, and zirconium materials into a crusher for crushing. After being crushed into granules, put the granules into a mixer and add water for stirring. The stirring time is 5 minutes to obtain mixed granules A;
[0030] b Put the SiO2 micropowder, heat-resistant steel fiber, and nano-barite powder into a ball mill and mix for 30 minutes to make it mix evenly and fully to obtain the mixture B;
[0031] c. Put the mixed particle A and the mixed material B into a vacuum mixer, add the binder and water, and stir for 40 minutes under vacuum conditions to obtain the mixed material C;
[0032] d Pour the mixture C into a clean fixed mould, use a vibrating rod to vibrate and shape in layers, and wait until the surface is flooded, and the product is ready;
[0033] The above raw materials are calculated by weight: 46 parts of mullite, 25 parts of brown cor...
Embodiment 3
[0038] A method for preparing a high-strength mullite castable, comprising the following steps:
[0039] a. Put mullite, brown corundum, and zirconium materials into a crusher for crushing. After being crushed into granules, put the granules into a mixer and add water for stirring. The stirring time is 8 minutes to obtain mixed granules A;
[0040] b Put the SiO2 micropowder, heat-resistant steel fiber, and nano-barite powder into a ball mill and mix them for 24 minutes to make them mix evenly and fully to obtain the mixture B;
[0041] c. Put the mixed particle A and the mixed material B into the vacuum mixer, add the binder and water, and stir for 45 minutes under vacuum conditions to obtain the mixed material C;
[0042] d Pour the mixture C into a clean fixed mould, use a vibrating rod to vibrate and shape in layers, and wait until the surface is flooded, and the product is ready;
[0043] The above raw materials are calculated by weight: 50 parts of mullite, 20 parts of ...
PUM
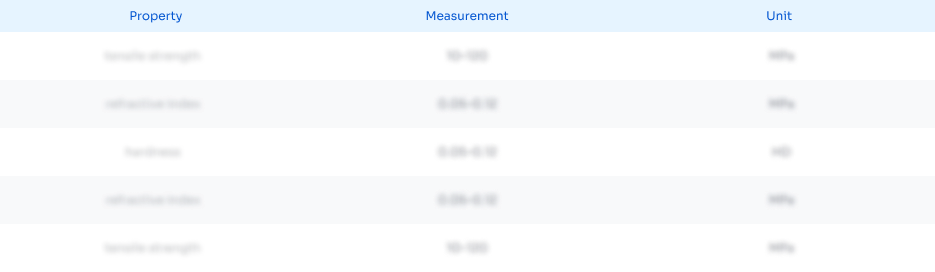
Abstract
Description
Claims
Application Information

- R&D Engineer
- R&D Manager
- IP Professional
- Industry Leading Data Capabilities
- Powerful AI technology
- Patent DNA Extraction
Browse by: Latest US Patents, China's latest patents, Technical Efficacy Thesaurus, Application Domain, Technology Topic, Popular Technical Reports.
© 2024 PatSnap. All rights reserved.Legal|Privacy policy|Modern Slavery Act Transparency Statement|Sitemap|About US| Contact US: help@patsnap.com