Electric braking electromechanical drive architecture for aircraft and braking force control method
A technology of braking control and drive control, applied in aircraft braking arrangements, control mechanisms, brakes, etc., can solve problems such as the deterioration of the force condition of the landing gear, the reduction of aircraft braking ability, and the loss of braking ability, so as to shorten the braking distance, prevent the The effect of deviating from the runway and improving safety
- Summary
- Abstract
- Description
- Claims
- Application Information
AI Technical Summary
Problems solved by technology
Method used
Image
Examples
Embodiment 1
[0043] In this embodiment, an aircraft with eight main wheels is used as the target aircraft, and a typical aircraft electric brake control and monitoring system is constructed, such as figure 2 As shown, multiple electromechanical actuators on each main brake wheel are controlled by different electromechanical drivers. On this basis, the aircraft electric brake electromechanical drive architecture and braking force control method of the present invention are introduced. In order to have a uniform brake pressing force between the brake disc and the static disc, to ensure the stability of the braking torque and the uniform wear of the disc surface, four electromechanical actuators are evenly distributed in the circumferential direction of the end face of the main brake wheel brake device. Universal applicability.
[0044] This embodiment includes a command control framework and a drive control framework.
[0045]The command control architecture includes the captain left brake...
Embodiment 2
[0055] This embodiment is a braking force control method for the electromechanical drive framework of the aircraft electric brake according to the present invention when the electric brake power supply unit, the electromechanical driver and the electromechanical actuator fail. The specific process is:
PUM
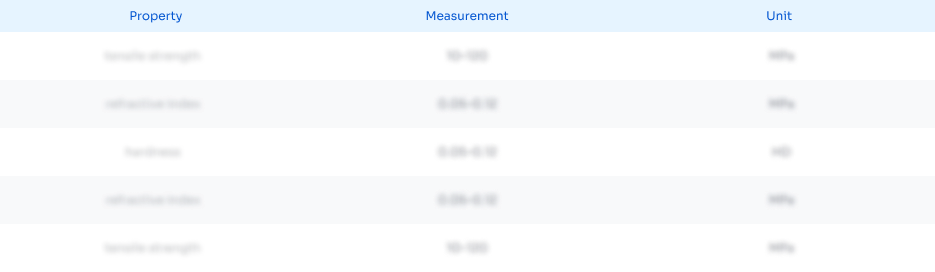
Abstract
Description
Claims
Application Information

- Generate Ideas
- Intellectual Property
- Life Sciences
- Materials
- Tech Scout
- Unparalleled Data Quality
- Higher Quality Content
- 60% Fewer Hallucinations
Browse by: Latest US Patents, China's latest patents, Technical Efficacy Thesaurus, Application Domain, Technology Topic, Popular Technical Reports.
© 2025 PatSnap. All rights reserved.Legal|Privacy policy|Modern Slavery Act Transparency Statement|Sitemap|About US| Contact US: help@patsnap.com