Mechanical arm control precision collaborative optimization method
A technology of collaborative optimization and control accuracy, applied in the directions of manipulator, program control, general control system, etc., can solve the problem of not being the optimal design of the system, and achieve the effect of improving the overall performance
- Summary
- Abstract
- Description
- Claims
- Application Information
AI Technical Summary
Problems solved by technology
Method used
Image
Examples
Embodiment Construction
[0068] The technology of the present invention will be further described below:
[0069] Such as figure 1 As shown, a method for collaborative optimization of control accuracy of a mechanical arm is characterized in that it includes:
[0070] Step 1: Perform configuration analysis and positive kinematics analysis of the robotic arm;
[0071] Step 2: Analyze the inverse kinematics of the robotic arm;
[0072] Step 3: Plan the end trajectory of the robotic arm;
[0073] Step 4: Space trajectory planning of the robotic arm joints;
[0074] Step 5: Topology optimization of the robotic arm rod;
[0075] Step 6: Cooperative optimization of control parameters;
[0076] Step 7: Comparison and verification.
[0077] The first step: the configuration analysis and positive kinematics analysis of the manipulator, including: according to the actual six-degree-of-freedom light-weight manipulator configuration, establish the mechanism diagram of the manipulator, and use the standard DH parameter method t...
PUM
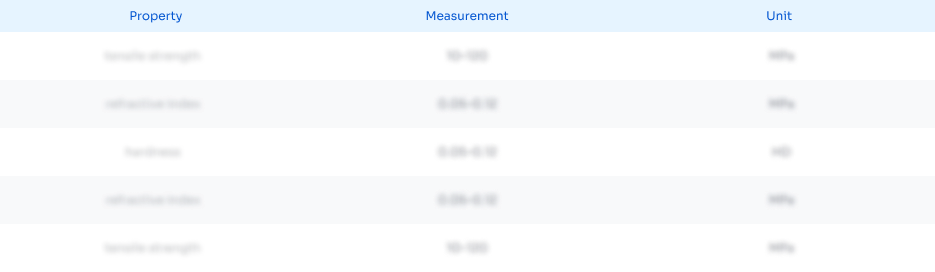
Abstract
Description
Claims
Application Information

- Generate Ideas
- Intellectual Property
- Life Sciences
- Materials
- Tech Scout
- Unparalleled Data Quality
- Higher Quality Content
- 60% Fewer Hallucinations
Browse by: Latest US Patents, China's latest patents, Technical Efficacy Thesaurus, Application Domain, Technology Topic, Popular Technical Reports.
© 2025 PatSnap. All rights reserved.Legal|Privacy policy|Modern Slavery Act Transparency Statement|Sitemap|About US| Contact US: help@patsnap.com