A production process of 3D printing resin
A 3D printing and production process technology, applied in the field of 3D printing, can solve the problems of low toughness, poor surface quality, and narrow application range, etc., to achieve improved tensile properties and bending properties, high heat resistance and bending resistance, Effect of reducing volume shrinkage
- Summary
- Abstract
- Description
- Claims
- Application Information
AI Technical Summary
Problems solved by technology
Method used
Image
Examples
Embodiment 1
[0030] A kind of production technique of 3D printing resin, comprises the steps:
[0031] (1) stirring
[0032] First, concentrated sulfuric acid and natural flake graphite are added to the reaction kettle, and then stirred. The stirring time is 10 minutes. At the same time, silver nitrate and potassium permanganate are slowly added, and then vigorously stirred, and left to stand for 90 hours after vigorously stirred. Obtain the mixed solution, the time of the vigorous stirring is 1h;
[0033] (2) Heating
[0034] Add water to the mixed solution, then heat the mixed solution and water to 95°C, then add 30% hydrogen peroxide to react for 10 hours, and filter after the reaction to obtain a graphite blank. The heating time is 20 minutes, and the filtered treatment Carry out washing afterward, the solution of described washing is deionized water and hydrochloric acid, and the massfraction of described hydrochloric acid is 4%;
[0035] (3) drying
[0036] Then the graphite blan...
Embodiment 2
[0046] A kind of production technique of 3D printing resin, comprises the steps:
[0047] (1) stirring
[0048] First, concentrated sulfuric acid and natural flake graphite are added to the reaction kettle, and then stirred, and the stirring time is 15 minutes, and silver nitrate and potassium permanganate are slowly added at the same time, followed by vigorous stirring, and left standing for 95 hours after vigorous stirring, Obtain the mixed solution, the time of the vigorous stirring is 1.5h;
[0049] (2) Heating
[0050] Add water to the mixed solution, then heat the mixed solution and water to 98°C, then add 30% hydrogen peroxide to react for 12 hours, and filter after the reaction to obtain a graphite blank. The heating time is 40 minutes, and the filtered treatment Carry out washing afterward, the solution of described washing is deionized water and hydrochloric acid, and the massfraction of described hydrochloric acid is 5%;
[0051] (3) drying
[0052] Then the gra...
Embodiment 3
[0062] A kind of production technique of 3D printing resin, comprises the steps:
[0063] (1) stirring
[0064] First, concentrated sulfuric acid and natural flake graphite are added to the reaction kettle, and then stirred. The stirring time is 20 minutes, and silver nitrate and potassium permanganate are slowly added at the same time, followed by vigorous stirring, and left standing for 100 hours after vigorous stirring. Obtain the mixed solution, the time of the vigorous stirring is 2h;
[0065] (2) Heating
[0066] Add water to the mixed solution, then heat the mixed solution and water to 100°C, then add 30% hydrogen peroxide to react for 14 hours, and filter after the reaction to obtain a graphite blank. The heating time is 60 minutes, and the filtered treatment Carry out washing afterward, the solution of described washing is deionized water and hydrochloric acid, and the massfraction of described hydrochloric acid is 6%;
[0067] (3) drying
[0068]Then the graphite...
PUM
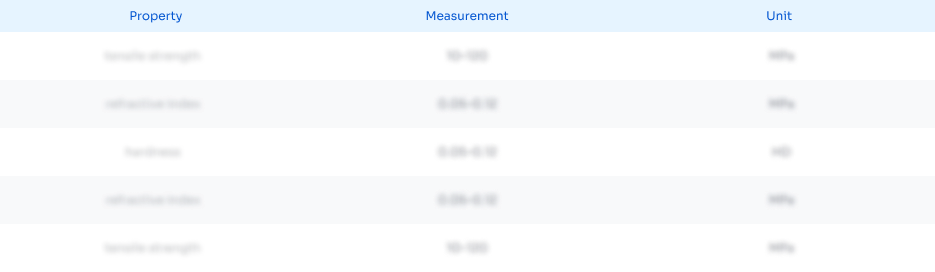
Abstract
Description
Claims
Application Information

- R&D
- Intellectual Property
- Life Sciences
- Materials
- Tech Scout
- Unparalleled Data Quality
- Higher Quality Content
- 60% Fewer Hallucinations
Browse by: Latest US Patents, China's latest patents, Technical Efficacy Thesaurus, Application Domain, Technology Topic, Popular Technical Reports.
© 2025 PatSnap. All rights reserved.Legal|Privacy policy|Modern Slavery Act Transparency Statement|Sitemap|About US| Contact US: help@patsnap.com