A cross-spinning strengthening forming method of titanium alloy thin-walled cylindrical parts
A forming method and technology for titanium alloys, applied in forming tools, metal processing equipment, manufacturing tools, etc., can solve the problems of low circumferential tensile strength and low axial tensile strength of titanium alloy thin-walled cylindrical parts, and achieve all directions. The effect of reducing anisotropy, increasing hoop strength, and weakening radial deformation texture strength
- Summary
- Abstract
- Description
- Claims
- Application Information
AI Technical Summary
Problems solved by technology
Method used
Image
Examples
specific Embodiment approach 1
[0024] Specific implementation mode one: combine figure 1 and figure 2 Describe this embodiment, the cross-spinning strengthened forming method of titanium alloy thin-walled cylindrical part in this embodiment, it is characterized in that: this method is carried out according to the following steps:
[0025] Step 1: Put the titanium alloy billet on the mandrel of the spinning machine and fix it, preheat the mandrel of the spinning machine and the titanium alloy billet, and spray evenly on the outer surface of the mandrel of the spinning machine and the outer surface of the titanium alloy billet Lubricant; the mandrel of the spinning machine is preheated to 150-200°C, and the titanium alloy blank is preheated to 350-400°C;
[0026] Step 2: preheat the mandrel and blank of the spinning machine to 650-850°C, and preheat the spinning wheel of the spinning machine to 100-150°C;
[0027] Step 3: Start the spinning machine for strong spinning;
[0028] Step 4: Change the rotation...
specific Embodiment approach 2
[0034] Embodiment 2: The difference between this embodiment and Embodiment 1 is that the material of the steel used for the wheel of the spinning machine and the mandrel of the press in Step 1 is 4Cr5MoSiV1. Other steps and parameters are the same as those in the first embodiment.
specific Embodiment approach 3
[0035] Embodiment 3: The difference between this embodiment and Embodiment 1 or 2 is that when the titanium alloy blank is placed on the mandrel of the spinning machine in step 1, there is a transition between the titanium alloy blank and the mandrel of the press Cooperate. Other steps and parameters are the same as those in Embodiment 1 or 2.
PUM
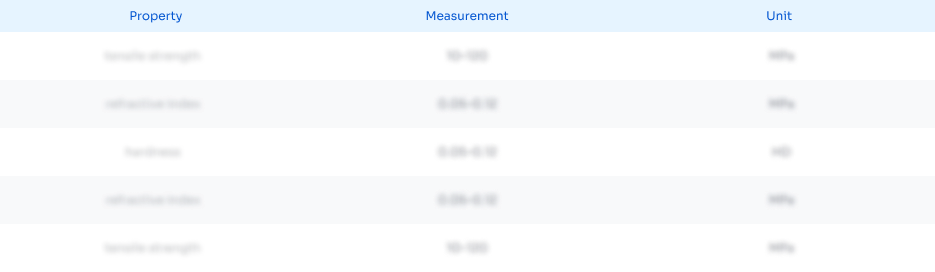
Abstract
Description
Claims
Application Information

- R&D Engineer
- R&D Manager
- IP Professional
- Industry Leading Data Capabilities
- Powerful AI technology
- Patent DNA Extraction
Browse by: Latest US Patents, China's latest patents, Technical Efficacy Thesaurus, Application Domain, Technology Topic, Popular Technical Reports.
© 2024 PatSnap. All rights reserved.Legal|Privacy policy|Modern Slavery Act Transparency Statement|Sitemap|About US| Contact US: help@patsnap.com