Change-material model test design method of load transfer characteristics of aircraft thin-wall structure
A technology for model testing and thin-walled structures, applied in design optimization/simulation, instruments, calculations, etc., can solve problems such as process control difficulties, increased test costs, and long material preparation cycles, achieving low prices, reduced design risks, and short material preparation cycles short effect
- Summary
- Abstract
- Description
- Claims
- Application Information
AI Technical Summary
Problems solved by technology
Method used
Image
Examples
Embodiment Construction
[0043] In order to make the objectives, technical solutions and advantages of the present invention clearer, the technical solutions in the embodiments of the present invention will be described in more detail below in conjunction with the drawings in the embodiments of the present invention.
[0044] When the thickness of the thin-walled structure of the aircraft is much smaller than the length and width (the ratio of thickness t to length or width b satisfies t / b≤(1 / 100~1 / 80)), it is in a state of plane stress (film stress) and can be Adjusts the scaling of the structure thickness within a range. The stress magnitude and stress distribution of the thin-walled structure of the aircraft are related to the Poisson's ratio of the material, but when the Poisson's ratio of the material selected for the model test is close to that of the prototype, the Poisson's ratio has little influence on the model test results, and the error is possible. controlled. Therefore, the present inve...
PUM
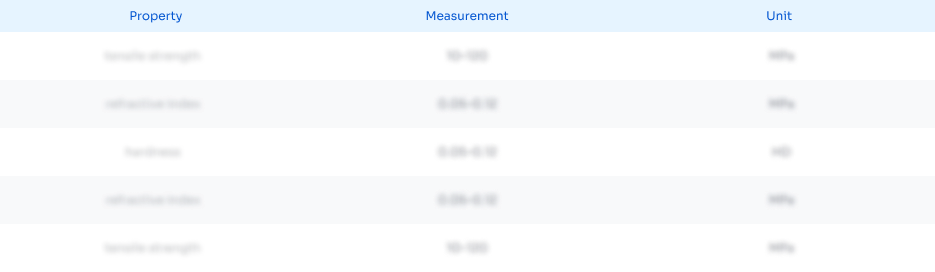
Abstract
Description
Claims
Application Information

- Generate Ideas
- Intellectual Property
- Life Sciences
- Materials
- Tech Scout
- Unparalleled Data Quality
- Higher Quality Content
- 60% Fewer Hallucinations
Browse by: Latest US Patents, China's latest patents, Technical Efficacy Thesaurus, Application Domain, Technology Topic, Popular Technical Reports.
© 2025 PatSnap. All rights reserved.Legal|Privacy policy|Modern Slavery Act Transparency Statement|Sitemap|About US| Contact US: help@patsnap.com