Black glaze for ceramics and preparation method thereof
A black glaze and ceramic technology, which is applied in the field of ceramic glaze production, can solve the problems of insufficient brightness and uneven color of the glaze surface, and achieve the effects of good gloss, stable color development, and increased yield
- Summary
- Abstract
- Description
- Claims
- Application Information
AI Technical Summary
Problems solved by technology
Method used
Examples
Embodiment 1
[0014] A kind of black glaze material for ceramics, according to the composition by weight: 18 parts of albite feldspar, 20 parts of goat rock, 15 parts of calcite, 8 parts of calcined ferric oxide, 15 parts of fluvo-aquic soil, 12 parts of grass ash, 6 parts of manganese powder Parts, 6 parts of barium carbonate.
[0015] According to the composition ratio of the ceramic black glaze of the present embodiment, the preparation method of the black glaze is that the black glaze is ball milled for 14 hours according to the mass ratio of raw material: ball stone: water=1.1: 1.5: 0.9, and the fineness is The 260 mesh sieve residue is less than 0.5%, and then the product is obtained.
[0016] Before ball milling, ferric oxide is calcined at high temperature.
[0017] Before ball milling, the goose and sheep mountain stone is roughly machined to 40-60 mesh.
[0018] The prepared black glaze is glazed on the body, and the temperature is gradually raised to 1230°C for high temperature...
Embodiment 2
[0020] A kind of black glaze material for ceramics, which is composed of 17 parts by weight of albite feldspar, 21 parts of goat rock, 14 parts of calcite, 8 parts of ferric oxide, 17 parts of fluvo-aquic soil, 13 parts of grass ash, and 5 parts of manganese powder , 5 parts of barium carbonate.
[0021] According to the composition ratio of the ceramic black glaze of the present embodiment, the preparation method of the black glaze is that the black glaze is ball milled for 12 hours according to the mass ratio of raw material: ball stone: water=1: 1.5: 0.7, and the fineness is The 260 mesh sieve residue is less than 0.5%, and then the product is obtained.
[0022] Before ball milling, ferric oxide is calcined at high temperature.
[0023] Before ball milling, the goose and sheep mountain stone is roughly machined to 40-60 mesh.
Embodiment 3
[0025] A kind of black glaze material for ceramics, which is composed of 16 parts by weight of albite feldspar, 22 parts of goat rock, 14 parts of calcite, 8 parts of ferric oxide, 16 parts of fluvo-aquic soil, 14 parts of grass ash, and 5 parts of manganese powder , 5 parts of barium carbonate.
[0026] According to the composition ratio of the ceramic black glaze of the present embodiment, the preparation method of the black glaze is that the black glaze is ball milled for 12 hours according to the mass ratio of raw material: ball stone: water=1: 1.5: 0.9, and the fineness is The 260 mesh sieve residue is less than 0.5%, and then the product is obtained.
[0027] Before ball milling, ferric oxide is calcined at high temperature.
[0028] Before ball milling, the goose and sheep mountain stone is roughly machined to 40-60 mesh.
PUM
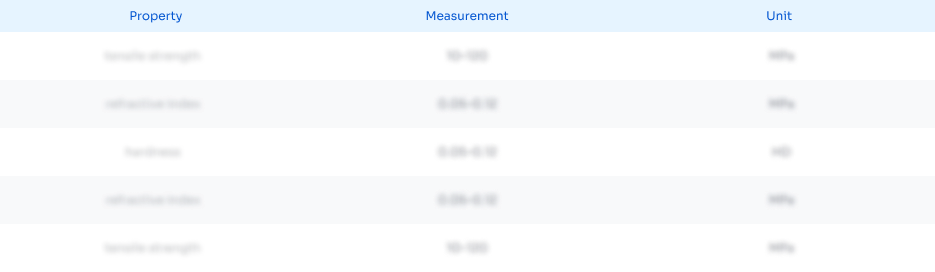
Abstract
Description
Claims
Application Information

- R&D
- Intellectual Property
- Life Sciences
- Materials
- Tech Scout
- Unparalleled Data Quality
- Higher Quality Content
- 60% Fewer Hallucinations
Browse by: Latest US Patents, China's latest patents, Technical Efficacy Thesaurus, Application Domain, Technology Topic, Popular Technical Reports.
© 2025 PatSnap. All rights reserved.Legal|Privacy policy|Modern Slavery Act Transparency Statement|Sitemap|About US| Contact US: help@patsnap.com