Manufacturing method of fluorosilicone rubber material for insulator
A technology of fluorosilicone rubber and manufacturing method, which is applied in the direction of organic insulators and rubber insulators, and can solve the problems of affecting the service life of insulators, reducing the hydrophobicity of materials, and hardening
- Summary
- Abstract
- Description
- Claims
- Application Information
AI Technical Summary
Problems solved by technology
Method used
Examples
Embodiment 1
[0018] By weight, 22 parts of fluorine rubber raw rubber, 59 parts of silicone rubber compound, 3 parts of diphenyl silicon glycol, 0.7 parts of trimethylsilyl perrhenate, 0.05 parts of 1,1-dimethyl silicon Hetero-11-crown-4, 0.02 parts of neodymium 1,1-trifluoroacetylacetonate, put them in a vacuum kneader, fully stir to obtain modified silicone rubber;
[0019] According to parts by weight, put the above 100 parts of modified silicone rubber into a vacuum kneader, break up the rubber material, add 33 parts of white carbon black and 2 parts of silicon glycol, stir evenly, and then discharge the material. Use an open rubber mixing machine. After molding, the mixed rubber is prepared and stored and allowed to stand; then, put the stored mixed rubber into an open rubber mixer, and add 123 parts of aluminum hydroxide, 3 parts of zinc oxide, and 0.03 parts of europium oxide according to the proportions. , 2 parts of hydroxy silicone oil and 1 part of vulcanizing agent are put into th...
Embodiment 2
[0021] By weight, 15 parts of fluorine rubber raw rubber, 45 parts of silicone rubber compound rubber, 2 parts of diphenyl silicon glycol, 0.1 part of trimethylsilyl perrhenate, 0.01 part of 1,1-dimethyl silicon Hetero-11-crown-4, 0.01 parts of neodymium 1,1-trifluoroacetylacetonate, put them in a vacuum kneader, fully stir to prepare modified silicone rubber;
[0022] According to parts by weight, put the above 100 parts of modified silicone rubber into a vacuum kneader, break up the rubber material, add 20 parts of white carbon black and 1 part of silicon glycol, stir evenly, and then discharge the material. Use an open rubber mixing machine. After molding, the mixed rubber is prepared and stored and allowed to stand; then, put the stored mixed rubber into an open rubber mixer, and add 100 parts of aluminum hydroxide, 1 part of zinc oxide, and 0.01 parts of europium oxide according to the proportions. , 1 part of hydroxy silicone oil and 0.5 part of vulcanizing agent are put in...
Embodiment 3
[0024] By weight, 35 parts of fluorine rubber raw rubber, 70 parts of silicone rubber compound, 5 parts of diphenyl silicon diol, 1 part of trimethylsilyl perrhenate, 0.1 part of 1,1-dimethyl silicon Hetero-11-crown-4, 0.1 part of neodymium 1,1-trifluoroacetylacetonate, put it in a vacuum kneader and stir it fully to obtain modified silicone rubber;
[0025] According to parts by weight, put the above 100 parts of modified silicone rubber into a vacuum kneader, break the rubber material, add 42 parts of white carbon black and 5 parts of silicon glycol, stir evenly, and then discharge the material. After molding, the mixed rubber is prepared and stored and allowed to stand; then, put the stored mixed rubber into an open rubber mixer, and add 140 parts of aluminum hydroxide, 5 parts of zinc oxide, and 0.1 parts of europium oxide according to the proportions. , 5 parts of hydroxy silicone oil, 3 parts of vulcanizing agent, put them into the vacuum kneader, mix evenly, and then thin ...
PUM
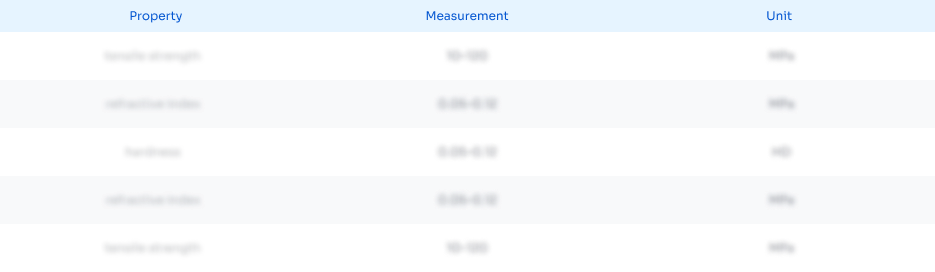
Abstract
Description
Claims
Application Information

- R&D Engineer
- R&D Manager
- IP Professional
- Industry Leading Data Capabilities
- Powerful AI technology
- Patent DNA Extraction
Browse by: Latest US Patents, China's latest patents, Technical Efficacy Thesaurus, Application Domain, Technology Topic, Popular Technical Reports.
© 2024 PatSnap. All rights reserved.Legal|Privacy policy|Modern Slavery Act Transparency Statement|Sitemap|About US| Contact US: help@patsnap.com