Molding sand
A technology of molding sand and halo sand, applied in the field of ore sand, can solve the problems of uneven condensation speed, poor effect, shrinkage cavities, etc., and achieve the effects of uniform condensation speed, lower use cost, and enhanced viscosity
- Summary
- Abstract
- Description
- Claims
- Application Information
AI Technical Summary
Problems solved by technology
Method used
Examples
Embodiment 1
[0010] A molding sand is composed of the following components in parts by weight: 15 parts of clay sand, 15 parts of quartz sand, 20 parts of hao sand, 20 parts of magnesia, 8 parts of bentonite, 5 parts of zeolite powder, 3 parts of rosin, and 2 parts of gypsum powder 5 parts, coal powder 5 parts, binder 25 parts, hardener 10 parts, starch 5 parts, water 10 parts.
[0011] Mix the above materials together and stir them evenly, then heat them, keep stirring them while heating until the temperature reaches 220°C, stop heating, and cool to normal temperature to get the finished molding sand.
Embodiment 2
[0013] A kind of molding sand is composed of the following components in parts by weight: 20 parts of clay sand, 20 parts of quartz sand, 22 parts of haosha, 22 parts of magnesia, 11 parts of bentonite, 7 parts of zeolite powder, 5 parts of rosin, and 4 parts of gypsum powder 7 parts of coal powder, 30 parts of binder, 13 parts of hardener, 7 parts of starch, and 12 parts of water.
[0014] Mix the above materials together and stir them evenly, then heat them, keep stirring them while heating until the temperature reaches 220°C, stop heating, and cool to normal temperature to get the finished molding sand.
Embodiment 3
[0016] A kind of molding sand, which consists of the following components by weight: 25 parts of clay sand, 25 parts of quartz sand, 25 parts of hao sand, 25 parts of magnesia, 15 parts of bentonite, 8 parts of zeolite powder, 6 parts of rosin, and 5 parts of gypsum powder 10 parts of coal powder, 35 parts of binder, 15 parts of hardener, 10 parts of starch, and 13 parts of water.
[0017] Mix the above materials together and stir them evenly, then heat them, keep stirring them while heating until the temperature reaches 220°C, stop heating, and cool to normal temperature to get the finished molding sand.
PUM
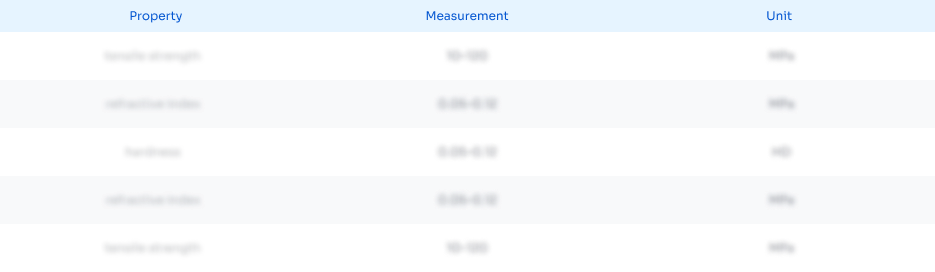
Abstract
Description
Claims
Application Information

- R&D Engineer
- R&D Manager
- IP Professional
- Industry Leading Data Capabilities
- Powerful AI technology
- Patent DNA Extraction
Browse by: Latest US Patents, China's latest patents, Technical Efficacy Thesaurus, Application Domain, Technology Topic, Popular Technical Reports.
© 2024 PatSnap. All rights reserved.Legal|Privacy policy|Modern Slavery Act Transparency Statement|Sitemap|About US| Contact US: help@patsnap.com