Sensorless DTC control method and control system of synchronous reluctance motor
A technology of synchronous reluctance motor and control method, applied in control system, vector control system, motor generator control and other directions, can solve the problems of increasing the economic cost of system firmware, difficult sensor setting, etc. The effect of good dynamic performance and high steady-state operation efficiency
- Summary
- Abstract
- Description
- Claims
- Application Information
AI Technical Summary
Problems solved by technology
Method used
Image
Examples
Embodiment Construction
[0069] The technical solution of the present invention will be further described in detail below in conjunction with the accompanying drawings.
[0070] Such as Figure 1-3 Shown, a kind of synchronous reluctance motor sensorless DTC control method, it comprises the following steps:
[0071] 1) Power collection, detecting the two-phase current output by the synchronous reluctance motor driver and the system bus voltage, combined with the motor stator resistance parameters and the voltage reconstruction method, to obtain the voltage, current and back EMF in the static coordinate system on the stator side of the driver;
[0072] 2) Observing and estimating, performing flux linkage observation, torque observation and rotational speed observation and estimation according to the power data obtained in step 1), and feeding back the corresponding results to the control optimization step, DTC control step and speed loop PI control step;
[0073] 3) speed loop PI control, adjust and c...
PUM
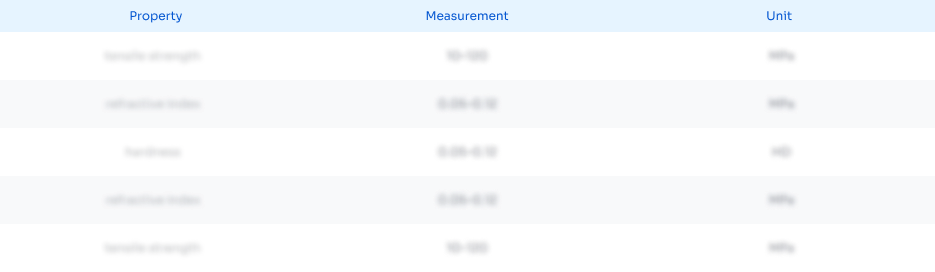
Abstract
Description
Claims
Application Information

- R&D Engineer
- R&D Manager
- IP Professional
- Industry Leading Data Capabilities
- Powerful AI technology
- Patent DNA Extraction
Browse by: Latest US Patents, China's latest patents, Technical Efficacy Thesaurus, Application Domain, Technology Topic, Popular Technical Reports.
© 2024 PatSnap. All rights reserved.Legal|Privacy policy|Modern Slavery Act Transparency Statement|Sitemap|About US| Contact US: help@patsnap.com