Combined car frame of car
A combined, frame technology, applied in vehicle components, upper structure, lower structure, etc., can solve the problems of adding vibration-absorbing and vibration-absorbing components, increasing the weight of the frame, increasing the weight of the frame, etc., to reduce the vibration-damping structure, residual The effect of less stress and reducing the quality of the whole vehicle
- Summary
- Abstract
- Description
- Claims
- Application Information
AI Technical Summary
Problems solved by technology
Method used
Image
Examples
Embodiment 1
[0035] as attached Figure 1-3As shown in the figure, the present embodiment provides a combined frame for a car, including a front section 1 of a frame body, a middle section 2 of the frame body, and a rear section 3 of the frame body that are fixedly connected to the front section 1 of the frame body in turn; the frame The front section 1 of the main body and the rear section 3 of the main body of the frame are on the same plane, and the front section 1 of the main body and the rear section 3 of the main frame are higher than the plane where the middle section 2 of the main frame is located, which is larger than the tire radius by 200mm-350mm, which not only makes the wheels jump There is enough space, and the center of gravity of the frame is further lowered to improve the stability of the car;
[0036] The front section 1 of the frame body is cast or forged from magnesium alloy, and includes two "I"-shaped magnesium alloy frame body front section longitudinal beams 7 and t...
Embodiment 2
[0045] The technical solution is the same as that of Embodiment 1, the frame is for SUV, and the total length of the longitudinal beams of the three-segment frame, namely the front section 1 of the frame body, the middle section 2 of the frame body and the rear section 3 of the frame body, is between 4400mm and 5000mm. , the wheelbase of the car is generally about 58% to 63% of the frame, that is, the wheelbase of the car is between 2552mm and 3150mm; the length of the longitudinal beam in the middle of the main body of the frame is 70% to 80% of the wheelbase of the model used, giving the wheels to jump. Leave enough space; the height of the raised part of the front and rear sections of the frame should be 200mm-350mm greater than the radius of the tires of the model used. The cross-section of the three-section frame is "I"-shaped, and its size is the same as that of the I-shaped steel.
[0046] The length of the longitudinal beam in the middle section of the frame body is 1....
PUM
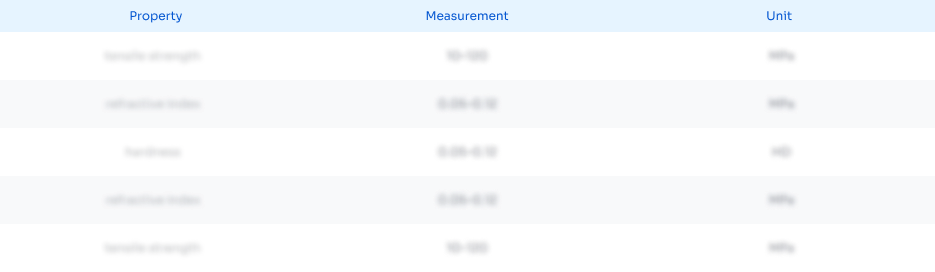
Abstract
Description
Claims
Application Information

- R&D Engineer
- R&D Manager
- IP Professional
- Industry Leading Data Capabilities
- Powerful AI technology
- Patent DNA Extraction
Browse by: Latest US Patents, China's latest patents, Technical Efficacy Thesaurus, Application Domain, Technology Topic, Popular Technical Reports.
© 2024 PatSnap. All rights reserved.Legal|Privacy policy|Modern Slavery Act Transparency Statement|Sitemap|About US| Contact US: help@patsnap.com