Flexible driver with controllable damping and used for robot joint
A robot joint and driver technology, applied in the field of robots, can solve the problems of uncontrollable compliance, delayed driving response, etc., and achieve the effects of simple structure, reduction of fluid impact, and prevention of damage
- Summary
- Abstract
- Description
- Claims
- Application Information
AI Technical Summary
Problems solved by technology
Method used
Image
Examples
Embodiment Construction
[0034] Further illustrate the present invention below in conjunction with accompanying drawing.
[0035] Such as figure 1 , 2 , 3, 4, 5, 6, 7 and 8, a compliant driver for controllable damping of robot joints, including a drive system and variable damping and variable stiffness structures. The driving system includes a stepping motor 1 and a hollow rotary platform; the base of the stepping motor 1 is fixed on one side of the outer ring 2 of the hollow rotating platform, and the outer ring 2 and the inner ring 3 of the hollow rotating platform form a revolving pair; the stepping motor 1 drives The inner ring 3 of the hollow rotating platform rotates; the variable damping and variable stiffness structure includes an output disc 4, an inner disc 8, an outer disc 18, a sealing ring 22, a plane torsion spring 5, a cross support frame 6, a first deep groove ball bearing 7, a second Two deep groove ball bearings 16, washers 17, nuts 20 and electric brushes; the brush stator 26 of t...
PUM
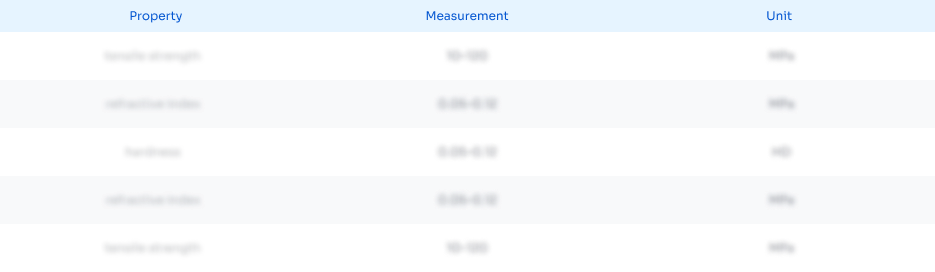
Abstract
Description
Claims
Application Information

- R&D
- Intellectual Property
- Life Sciences
- Materials
- Tech Scout
- Unparalleled Data Quality
- Higher Quality Content
- 60% Fewer Hallucinations
Browse by: Latest US Patents, China's latest patents, Technical Efficacy Thesaurus, Application Domain, Technology Topic, Popular Technical Reports.
© 2025 PatSnap. All rights reserved.Legal|Privacy policy|Modern Slavery Act Transparency Statement|Sitemap|About US| Contact US: help@patsnap.com