Main shaft assembly of continuous copper extruding machine
A technology of extruder and main shaft, applied in the field of main shaft assembly of copper continuous extruder, can solve the problems of large temperature stress, uneven temperature distribution of extrusion wheel, falling off (dropping iron, etc.)
- Summary
- Abstract
- Description
- Claims
- Application Information
AI Technical Summary
Problems solved by technology
Method used
Image
Examples
Embodiment Construction
[0015] Such as Figure 1 to Figure 3 As shown, the main shaft assembly of the copper continuous extrusion machine includes the mandrel 1, the inner shaft sleeve 2, the inner wheel 3, the outer wheel 5, the outer shaft sleeve 6, the bearing 7, the pressure sleeve 8, the extrusion wheel 9 and the hydraulic nut 10. The inner shaft sleeve 2 and the outer shaft sleeve 6 are respectively installed on the outside of the mandrel 1, the bearing 7 is installed outside the inner shaft sleeve 2 and the outer shaft sleeve 6, the inner wheel 3 is installed inside the inner shaft sleeve 2, and the outer wheel 5 Installed on the inside of the outer sleeve 6, the pressure sleeve 8 is installed on the outside of the outer sleeve 6, the squeeze wheel 9 is installed between the inner wheel 3 and the outer wheel 5, and the hydraulic nut 10 is installed on the outside of the pressure sleeve 8 and threaded with the mandrel 1 Auxiliary connection, the mandrel 1 is provided with an axial water inlet 1...
PUM
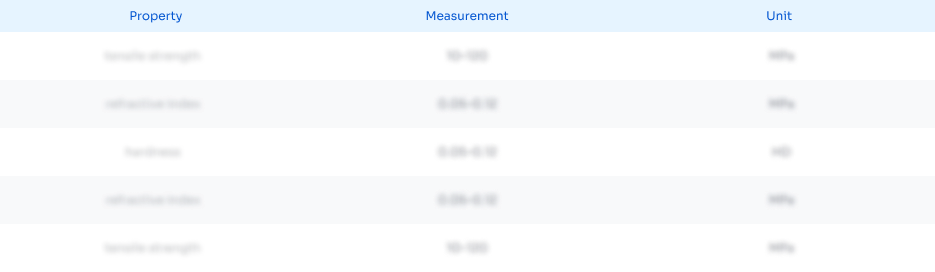
Abstract
Description
Claims
Application Information

- Generate Ideas
- Intellectual Property
- Life Sciences
- Materials
- Tech Scout
- Unparalleled Data Quality
- Higher Quality Content
- 60% Fewer Hallucinations
Browse by: Latest US Patents, China's latest patents, Technical Efficacy Thesaurus, Application Domain, Technology Topic, Popular Technical Reports.
© 2025 PatSnap. All rights reserved.Legal|Privacy policy|Modern Slavery Act Transparency Statement|Sitemap|About US| Contact US: help@patsnap.com